|
|
|
Reference
Publication:
Chandra, Subrato, Neil Moyer, Danny Parker, David Beal,
David Chasar, Eric Martin, Janet McIlvaine, Ross McCluney,
Andrew Gordon, Mike Lubliner, Mike McSorley, Ken Fonorow,
Mike Mullens, Mark McGinley, Stephanie Hutchinson, David
Hoak, and Linda Tozer. Building America Industrialized
Housing Partnership, Annual Report - Fourth Budget Period.
04/01/03-03/31/04. |
|
|
Building
America Industrialized Housing Partnership, Annual
Report - Fourth Budget Period |
|
|
Subrato
Chandra, Neil
Moyer, Danny
Parker, David
Beal, David
Chasar, Eric
Martin, Janet
McIlvaine, Ross
McCluney, Andrew
Gordon, Mike
Lubliner, Mike McSorley, Ken
Fonorow, Mike
Mullens, Mark
McGinley, Stephanie
Hutchinson, David
Hoak, and Linda Tozer |
|
Florida
Solar Energy Center |
|
|
|
TASK
2. RESEARCH
2.1
Moisture and IAQ Research
FSEC
conducted moisture and indoor air quality research to help
eliminate the most serious problems plaguing HUD Code homes
in the Southeast. To assist the industry, researchers performed
diagnostic tests in problem homes, fixed the problems, and
evaluated the effectiveness of the problem corrections by
conducting pre and postfix short-term tests and related activities.
- Bossier
City, Louisiana Experiments
In
2001, the BAIHP team conducted research on two homes to define
how tight ducts and a prototype Coleman heat pump
(proprietary technology) affect energy use and moisture control
in a hot, humid climate. FSEC, in collaboration with Fleetwood
Homes, York International Manufactured Housing Division (now
Stylecrest Sales), and Coleman, monitored two
nearly identical side-by-side homes in Bossier City, Louisiana.
The homes contained different air conditioning systems. House
A used a standard split air conditioner, while House B used
the Coleman prototype unit (a more efficient, two-speed split
air conditioner).
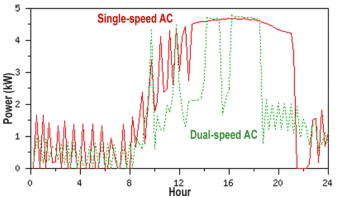 |
Figure
48. Power draw over a 24-hour period,September 2,
2000. |
Figure
48 (on left) shows the reduced power draw of the two-speed
compressor (green, dotted line) over a 24-hour period on September
2, 2000. With the unit operating at low-speed for most of
the day, the cooling energy savings were 28% when compared
to the energy use in House A. Average daily cooling energy
was reduced by about 12% over the monitored period. An added
benefit of the two-speed air conditioner was 20% greater moisture
removal on days with an outdoor dewpoint above 60F.
Savings
from Duct Repair and POS Ventilation: In addition to
comparing one house to the other, the BAIHP team also compared
home performance before and after ductwork and ventilation
system changes were made.
To
make the comparison, duct and other leaks were sealed in both
houses until the two were equally airtight. The ventilation
method in each home also was changed from exhaust-only to
a positive pressure system (POS). With exhaust-only ventilation,
bathroom fans removed stale air from the home which caused
fresh air to be pulled in through the building envelope.
To simulate occupant use, two bath exhaust fans were operated
by a timer for three hours in the morning and six hours in
the evening.
In
contrast to exhaust ventilation, the POS system introduced
a small amount of fresh air on the return side of the air
conditioning cooling coil. A POS system was installed in
each home at the same time the ducts were repaired. Subsequent
monitoring looked at the effects of this alternate ventilation
system. Tightening the ducts and installing a POS ventilation
system resulted in an 18% and 37% cooling savings in the two
homes. Only about 2% of these savings were attributable to
the ventilation system change, the remaining savings are a
result of duct repair.
- Building
Science and Moisture Problems in Manufactured Housing
Figure
49 shows one-half of a manufactured home recently completed
at the factory. These homes have a permanent steel chassis
attached below the floor. After production, homes may travel
a few hundred miles, hauled by truck, before final setup.
The homes are setup by placing blocks under the steel I-beams
and anchoring the beams firmly to the ground. A skirting covers
the blocks and steel frame in a fully setup home. (Please
see Figure 50.)
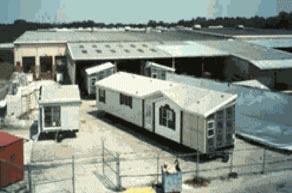 |
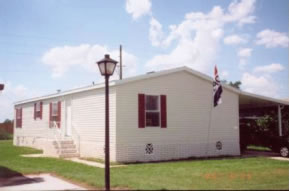 |
Figure
49. Manufactured home production. |
Figure
50. A fully setup two-section manufactured home with
skirting. |
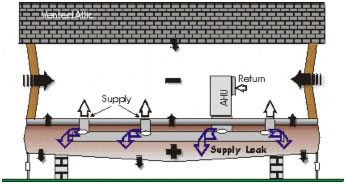 |
Figure
51. Pressure field and unintentional airflow created
by supply duct leaks. |
Manufactured
homes are typically heated or cooled by a system of ductwork,
which delivers hot or cold air from the air handler unit (AHU).
The ductwork can be in the attic or in the belly cavity of
the home. The ducts are typically made of aluminum or fiberglass
trunk lines which supply air to the floor registers through
in-line boots or flex ducts. The boots or ducts terminate
at perimeter registers on the floor. Supply duct leaks represent
one of the biggest causes of moisture in manufactured homes.
(Please see Figures 51, 52, and 53.) Poor design and construction
leave holes at the AHU connection to the main trunk, and where
the boots connect to the trunk, supply registers, end caps,
cross-over duct connections, and other connection points.
When the AHU blows air, some air leaks into the belly and
eventually to the outside through belly board tears. This
loss of air creates a negative pressure inside the house and
a positive pressure in the belly. The negative pressure pulls
outside or attic air into the house through cracks and crevices
which connect the inside of the house to the outside or to
the attic. During northern winters, this outside air is cold
and dry and its entry increases occupant discomfort and heating
energy use.
During
summer in the Southeastern US, the air is consistently at
or above the dewpoint of 75. If a homeowner keeps their
home thermostat set below this 75F dewpoint, the moisture
laden outside air condenses as it comes into contact with
the cold inside surfaces. If it condenses behind an impermeable
surface such as vinyl flooring or wallpaper, serious mold,
mildew, and floor buckling problems can result.
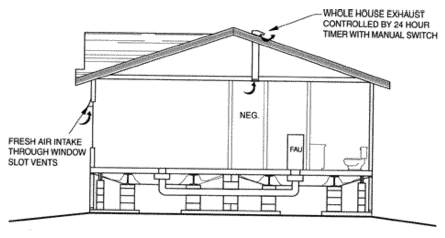 |
Figure
52. Cross section showing foundation support, crossover
duct, and one type of ventilation system in a manufactured
home. (Illustration credit: 1997 Northwest Energy Efficient
Manufactured Home Program In-Plant Inspection Manual) |
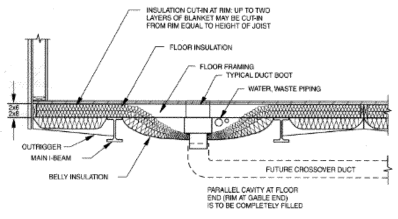 |
Figure
53. Floor and belly area with supply ducts. These
ducts supply conditioned air to all rooms through floor
vents, a common system in manufactured homes.(Illustration
credit: 1997 Northwest Energy Efficient Manufactured Home
Program In-Plant Inspection Manual) |
Many manufactured and site-built homes have
only a single return and, therefore, very little return air
transfer (basically via the undercut at the bottom of interior
doors). When interior doors are closed, rooms off the main
body (e.g., bedrooms) become pressurized and the main body
of the house depressurizes. Even though negative pressures
are usually only one to three Pascals (Pa) - they can cause
serious problems in a home.
Researchers use a calibrated fan called a
ductblaster to measure duct leakage. The ductblaster is attached
to the return grill or the crossover duct opening (Figure
54) and all supply registers are masked off and the fan is
turned on. Once the house ductwork reaches -25 Pa, airflow
through the fan is read (in CFM). The resultant measure is
the total duct leakage. In good airtight ductwork, total duct
leakage (CFM@25 Pa) should be less than 6% of the homes square
footage.
A second duct leakage measurement conducted,
measures leakage to the outside. This leakage is calculated
by depressurizing the entire house to -25 Pa with a blower
door, then adjusting the ductblaster flow so there is no pressure
difference between the house and the ducts. This measurement
is a true indicator of duct air loss to the outside and is
used in energy calculations for estimating the energy loss
from leaky ducts. In good duct systems, duct leakage to the
outside (in CFM) is less than 3% of the home's square footage.
The battery of tests run in a problem house
typically include measuring the airtightness of the house
with a blower door, depressurizing the house to -50 Pa. At
that time, the house to belly and belly to crawlspace pressures
also can be measured. Researchers also test pressure differentials
caused by AHU operation and closed interior doors. An additional
measurement of duct leakage, called pressure pan, is conducted
on some houses to pinpoint specific registers which might
have large leaks. In this measurement the house is first
depressurized to -50 Pa and all the register vents are unmasked.
Then the registers are covered one by one and the pressure
difference between the covered register and the house is measured.
A zero reading indicates no leakage at that register. Readings
over one Pa indicate a sizeable leak that should be repaired.
|
Disclaimer:
This report was prepared as an account of work sponsored by an agency
of the United States government. Neither the United States government
nor any agency thereof, nor any of their employees, makes any
warranty, express or implied, or assumes any legal liability
or responsibility for the accuracy, completeness, or usefulness
of any information, apparatus, product, or process disclosed,
or represents that its use would not infringe privately owned
rights. Reference herein to any specific commercial product,
process, or service by trade name, trademark, manufacturer,
or otherwise does not necessarily constitute or imply its endorsement,
recommendation, or favoring by the United States government
or any agency thereof. The views and opinions of authors expressed
herein do not necessarily state or reflect those of the United
States government or any agency thereof.
|