TRIP REPORT
TITLE
Problem Home Inspection - Southern Florida
TRIP DATE
November 6, 2002
INTRODUCTION
This
home was built in February of 2002 and occupied in
April. In June, homeowner noted soft spots in kitchen
floor. The home was inspected in August.
At that time, they found mold and moisture in
the floor of the kitchen/dining area. No replacements
were made. Homeowner reports that the belly was cut
extensively.
Homeowner now reports moldy smell in Bath 2, warped
kitchen/dining area, and a shift in the levelness of
the bathtub in the master bathroom.
DESCRIPTION
The
home is a 26' x 44' doublewide building with 3-bedrooms
and 2 baths enclosing about 1,100 square feet of living
space. No shading or landscaping was present.
The
crawlspace skirting appears to be standard vinyl skirting.
The ground around the skirting is damp though homeowners
report that there hasn't been any rain for several days.
Homeowner
reports the following operating conditions:
- 3
full time adult occupants
- 2
indoor dogs
- Thermostat is kept at
72° during the day and 74° at night (found
at 70°)
- Bedroom
doors are kept closed during the day.
- BR
2 and BR3 are closed at night. MBR is sometimes closed
at night.
- Seldom
run exhaust fans when not in room.
The ventilation air requirement is met with the use of
an exhaust fan located in the utility room. Heating and
cooling is accomplished with a central forced air system
with the ducts located in the attic connected to a packed
heating and cooling unit.
OBSERVATIONS (SEE PHOTOS)
- A
visual inspection of the property and equipment revealed:
- Supply
registers were not dirty and no condensation or water
stains were present.
- The
coil in the packaged unit was relatively clean.
- No
mold or moisture was present at the marriage line
ceiling joint.
- Sections
of the kitchen floor were warped.
- Black
mold growth was evident over the entire surface of the
sub floor in the kitchen,
- The
belly board was torn extensively near the supply and
return duct entry points.
- A tear approximately 2' by 5' was present at the marriage line
near the kitchen.
- No
ground cover was present in the crawl space.
- Belly
under hall bath had accumulated several gallons of
water.
- Mold
growth on exposed sub floor around dryer vent exit
hole in floor of utility room (see moisture measurement
table).
Temperature and relative humidity measurements suggest
a significantly damp crawl space (see table) while a Delmhorst
moisture meter showed high moisture levels in all floors
manifesting mold. Significant moisture levels were also
found in the utility room exterior wall and the shower
portion of the hall bathroom plumbing wall.
Air
Conditions |
Location |
Temperature |
Relative
Humidity |
Outside |
93°F |
52% |
Crawlspace |
83°F |
72% |
Inside |
75°F |
46% |
TESTING
Description
FSEC's
testing protocol establishes the integrity of the building
envelope and the duct system. These tests assist in
the determination of air-transported moisture that can cause
severe damage to building components, increase energy consumption
and decrease occupant comfort. Three tests using a
blower door and a duct blaster are performed. The first
test employs the blower door and establishes a leakage rate
for the house at a specific pressure (air changes per hour
at 50 pascals (Pa) or ACH50). (250 Pa is equal to 1inwc
or 6800 pa is equal to 1psi). The next two tests use
the duct blaster and yield the leakage rate of the duct
system in a similar manner (cubic feet per minute of air
leakage at 25 pascals (Pa) or CFM25). One test measures
the total leakage from the duct system to the interior and
exterior of the building (CFM25total) and the
second test measures leakage to the exterior of the building
only (CFM25out). For a duct system to be considered
to be "essentially leak free", the CFM25out
must be a number that is less than 3% of the conditioned
floor area (Percent Leakage = CFM25out / conditioned
area. X 100 >= 3%) or the CFMtotal must be less than
5% of the rated air handler flow.
The
testing protocol continues with a series of pressure differential
tests across the building envelope and various zones within
the building as defined by interior doors. The pressure
differences are created by either normal operation of the
building's HVAC equipment or the operation of the blower
door test equipment. Ideally, the pressure differentials
created across the building envelope and bedroom doors should
be close to neutral (below 2 Pa).
Blower door test and results
A
blower door test was done to determine the airtightness
of the building envelope. A series of building pressures
and associated airflows were recorded. This provides
the necessary inputs to determine the CFM50 and ACH50
of the house.
Blower
Door Test
CFM50
= 880 ACH50 = 5.65
ACH50
= (CFM50*60)/house volume. |
For
reference, most new homes of today have an airtightness
of approximately 0.75 to 1 CFM50 per square foot of floor
area. In this case, the house has an air tightness
of about 0.80 CFM50/sqft.
Duct test
A
duct system airtightness test was also completed.
A duct tester was attached to the air handler unit.
The supply registers were temporarily sealed off and the
system was then depressurized to 25 pascals. The total
and outside leakage flow components were measured.
An airtight duct system would have zero leakage or both
the CFM25total and CFM25out would
be 0. An "essentially leak free" duct would
have a CFM25out >= 33* (CFM25out
/ conditioned area. X 100 >= 3%).
Duct
System Airtightness (Aug 12) |
CFM25total =
141 |
*CFM25out =
71
(NOT
essentially leak free) |
Pressure diagnostic testing
Pressure differential measurements were completed to determine
a magnitude and direction of flow across the envelope when
the air handler fan operates. The effect of interior door
closure on the main body of the home was also measured
when the air handler fan operated.
Pressure
Diagnostics w ith AHU
(Note:
the winds were moderate) |
Condition |
Pressure
(main wrt out) |
All
fans off |
+1.5
pa |
AHU
on |
0
pa |
AHU
on & all interior doors closed |
-3
pa |
The pressure difference was also measured across each
closed door when the air handler fan was operating (all
supply registers were open and exhaust was off).
closed
doors |
Pressure
(room wrt main) |
Master
bedroom |
+
8.5 pa |
Bedroom
#2 |
+
1.5 pa |
Bedroom
#3 |
+
2.2 pa |
Conclusions
The problems with mold under the vinyl flooring throughout
the house are primarily due to moisture intrusion from
the exterior ambient environment, which enters (or tries
to enter) the house by two distinct methods:
• Diffusion
through materials and/or
• Air transport (driven
by inadequate return air pathways) through various penetrations
in the floor and wall interfaces. These include dryer
exhaust, electrical and plumbing penetrations and other
cracks and connections.
Where does the moisture come from?
The ground is a source of moisture under all homes. A
continuous vapor barrier ground cover prevents ground moisture
from rising into the crawl space. Crawl space ventilation
allows moist air to exit the crawl space to the outside.
When neither is present, the warm moist air (see table
of measurements) is trapped in the crawl space and enters
the house by diffusion.
Bulk water, such as rain, can contribute to the moisture
level in the crawl space. And in this home, a plumbing
compromise in the hall bath introduced water into the belly
(which held several gallons of water) creating a direct
path for diffusion into the house.
Diffusion:
A
vapor barrier or retarder, such as vinyl wall or floor
coverings, can interrupt the diffusion process or water
movement through a material. If an interior vapor
barrier (kitchen linoleum or vinyl wall covering) is at
a temperature below the dewpoint temperature of the outside
or crawlspace air and that air comes into contact with
that surface, then condensation will most likely occur.
The temperature of interior vapor barriers such as vinyl
flooring and wall coverings can become even colder when
cold air condition supply air is brought into contact with
them. This may be the cause of the very wet east wall in
the master bedroom where the diffuser was aimed primarily
toward that wall, making it even colder than the surrounding
air and accelerating condensation. The crawl space air
is the suspected source of moisture involved in the diffusion
process in the floors.
Air Transport:
The homeowners report operating the home with the interior
doors closed a significant portion of time. A negative
pressure of -3 pascals wrt outside was measured with interior
doors closed indicating insufficient return air pathways
from bedrooms, specifically the Master Bedroom which registered
an unusually high +8.5 pascals wrt house. This consequential
negative pressure in the main body of the house can induce
infiltration of warm moist outside air.
RECOMMENDATIONS
NOTE: All plumbing repairs should be completed
prior to implementing recommendations. All wet materials
should be removed during plumbing repair.
HVAC:
- Sufficient
return air pathways should be installed in all bedrooms.
- Inspect
crawlspace ducts for condensation at the collars. Ensure
collars are properly insulated.
- Encourage
homeowners to set thermostats at 78 degrees or higher
when in a cooling mode.
Crawlspace:
- If
standing water is present or evident, identified
the source and take steps to prevent future occurrence.
Remove all standing water.
- The
ventilation of the crawlspace should be increased
to at least one square foot per fifty square feet of
floor area. Lattice or brickwork is best with nearly
50% open area.
- A ground cover, such
as 6-mil visqueen or plastic sheathing should be laid on
the exposed soil. This should cover at least 90%
of the exposed area and should be installed and protected
so as to preclude the possibility of water accumulating
during heavy rainstorms. Joints should be lapped.
- Prevent
roof run-off from entering crawlspace during heavy downpours.
Rain Gutters will be very helpful as long as the run-off
is directed well away from the home.
Floor assembly:
- All
damaged, molded, and wet floor material should be
replaced. Plywood decking is preferred. Any wet floor
insulation should also be replaced.
- The
floor cavity should be thoroughly dry and free of mold
prior to replacement of floor assembly materials.
- The belly wrap should
be 100% sealed with a material that will last the life
of the building. This will help prevent air-transported
moisture from entering the floor assembly.
Address questions or comments to:
Dave Chasar - 321-638-1453, dchasar@fsec.ucf.edu
Or
Janet McIlvaine 321-638-1434, janet@fsec.ucf.edu
PICTURES
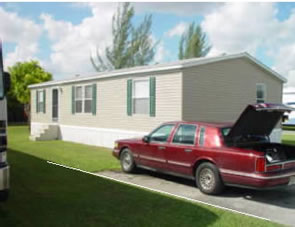
|
|
Skirting allowed
limited ventilation of crawlspace. No ground cover
present. |
Vinyl flooring
(kitchen) folded back to reveal extensive mold on
subflooring and floor back. |
|
|
Accumulated
water draining from belly board under hall bath and
kitchen due to plumbing leak.
Crawl
conditions: 83°F DB, 72%
RH, 74°F DP |
Plumbing supply
leak at hall bath was primary source of moisture
problems. |