Annual
Report
BUILDING
AMERICA INDUSTRIALIZED HOUSING PARTNERSHIP
WSU
Energy Program, IDWR, OOE
April
1, 2002 - March 30, 2003
TASK
1. TECHNICAL ASSISTANCE AND RESEARCH
Subtask
1.1 Technical Assistance
Super
Good Cents/Natural Choice/Energy Star (SGC/NC/E-Star)

Washington
State University Energy Program (WSU), together with partners
Oregon Office of Energy and Idaho Department of Water Resources,
Energy Division, continued to provide technical and research
support to the Super Good Cents/Natural Choice/Energy Star
(SGC/NC/E-Star) program in the Pacific Northwest. The SGC/NC/E-Star
program involves 20 plants in three states, hundreds of
retailers and thousands of homebuyers.
The
chart and table below show, by program year, the number
of homes produced with technical assistance from BAIHP,
as well as the number of homes submitted for Energy Star
designation by BAIHP staff.
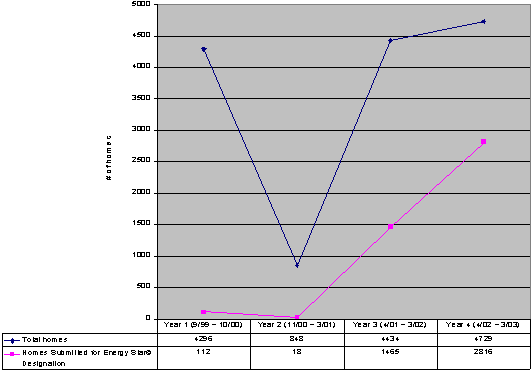 |
Figure
1. Homes produced with technical assistance from BAIHP,
along with
BAIHP homes submitted for Energy Star designation. |
The sharp decline in total production and Energy Star designation
during Year 2 was due to several factors. The SGC/NC/E-STAR
program had experienced a decline in penetration rates over
the preceding 5 years, and the project "year" was shortened
to 5 months (typically the lowest producing months for the
manufactured housing industry.)
The
increase in total production during Years 3 and 4 was due
to several factors, including an increased consumer awareness
of energy issues due to the Northwest's energy crisis in
Year 3. In addition, BAIHP staff has continued to work
to increase awareness within the manufactured housing industry
of the marketing value of energy efficiency, increase participation
by utilities in incentive programs, and promote the co-branding
of SGC/NC with Energy Star.
The
increase in Energy Star designations is due to refinement
of the SGC/NC duct sealing specifications, resolving a discrepancy
between the SGC/NC specifications with Energy Star's duct
sealing protocols. While this question was being resolved,
BAIHP staff did not submit homes to DOE for Energy Star
designation. In addition, during years 3 and 4, all 20
of the Northwest manufacturers signed Energy Star partnership
agreements.
SGC/NC/E-STAR
program activities include:
Problem
Homes: In offering technical support to owners of over
100,000 homes built since 1990, the staff answers questions
from homeowners, manufacturers, retailers and others. In
Year 4, staff from Washington, Oregon and Idaho responded
to over 70 phone calls and conducted 15 field visits. The
number of problem home field visits has significantly decreased
over the history of the program, in large part because of
manufacturer's and installer's increased awareness of the
SGC/NC/E-Star specifications, and the requirement that manufactured
home installers be certified in Washington and Oregon.
BAIHP
staff participated in quarterly meetings of the Washington
State Manufactured Housing Technical Working Group, which
coordinates the certification of manufactured housing set-up
crews. During Year 4, exactly 100 set-up crew personnel received
the training and certification.
A
consistent issue in the field continues to be excessive duct
leakage, due in large part to failures of butyl duct tape.
These findings were brought to the attention of the NFPA-501
Mfg Housing Standards committee, resulting in a successful
proposal to revise the duct sealing specifications in the
NFPA-501 standard.In-Plant Inspections: On a quarterly
basis, BAIHP staff visits each of the manufactured housing
plants to verify compliance with SGC/NC/E-Star specifications. Inspections
include a plant audit, ventilation system testing, and troubleshooting
construction-related problems with plant staff and independent
inspectors. Consistent issues in the plant include
wall insulation compression or voids due to improper cutting
of batts, attention to duct installation and air sealing. In
Year 4, BAIHP staff conducted quarterly in-plant inspection
at Valley Manufactured Housing in the company of local utilities,
DOE, BPA and PNNL personnel, with the goal of fostering closer
ties between the industry and utilities.
Refinement
of SGC/NC standards: BAIHP staff have been working to refine
the existing SGC/NC specifications, in large part to innovative
building technologies researched in BAIHP.
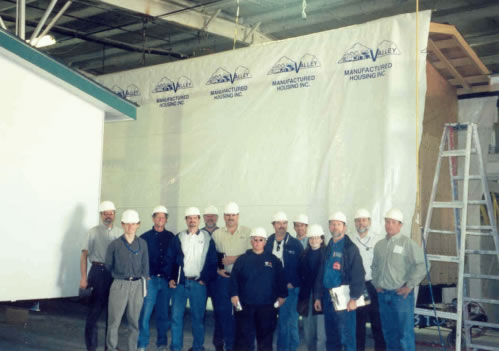 |
Figure
2. Quarterly plant inspection in the company
of representatives from utilities, DOE, BPA and PNNL
at Valley Manufactured Housing in Sunnyside Washington. |
As part of the specification revision, BAIHP staff have been working with EPA
and other regional partners on Worked with EPA to clarify the equivalency of
SGC/NC with Energy Star. In Year 4, BAIHP staff developed a new Energy
Star compliance path for climate zone 2 that doesn’t require a heat pump. The
non-heat pump path uses a heat recovery ventilation system, a .93 EF hot water
heater and tighter ducts and envelope. In Year 5, the revised specifications
will be proposed to and voted on by the manufacturers.
SGC
Random Home Testing: In Year 1, staff in Idaho and
Washington field-tested 49 SGC/NC homes built in 1997-98. In
Year 2, analysis of field test data confirmed some improvements
to home set-up procedures and air leakage control, while
highlighting a need to improve duct tightness and ventilation
system operation (through homeowner education.) In
Year 3, BAIHP staff produced an updated homeowner ventilation
brochure. During Year 4, BAIHP staff worked with
Ecotope to develop a valid sample for the next round
of field testing, and began to develop the field testing
protocol. The testing is scheduled for summer of
Year 5.
Transition
to mastic: By the end of Year 4, more manufacturers
eliminated the use of butyl tape for duct sealing, and
implemented mastic. Fleetwood Homes of Washington,
Marlette, Palm Harbor Homes, and Guerdon have adopted
mastic. Testing in-plant has indicated significant
improvement in the duct leakage rates of these homes. During
Year 5, BAIHP staff will continue to document the improvement
in duct leakage rates in-plant and in the field.
Duct
Workshops: In Year 2, workshops in Oregon and Washington
focused on improved duct installation and inspection
oversight, particularly on the use of mastic as a sealing
strategy for ductwork joists. Manufacturers Palm
Harbor Homes, Fleetwood Homes (Washington and Oregon)
and Valley Manufactured Housing participated. In
Year 3, these same manufacturers participated, as well
as Fuqua Homes, Marlette, and all of the Idaho manufacturers.
In
Year 4, BAIHP staff continued to provide these workshops,
working in partnership with BAIHP partner Flexible Technologies
to demonstrate the added value of their innovative duct
sealing technologies.
Blown
Cellulose Floor Insulation: Industry partner Engineered
for Life (EFL, formerly Greenstone) has been working
with SGC/NC/E-STAR manufacturers to validate a hybrid
insulation system composed of one R-11 belly blanket
and R-22 blown cellulose insulation. The goal is
to optimize installed R-value and minimize material and
labor costs. The hybrid system eliminates over-compression
and reduces the chance of leakage during transport and
set-up. Fleetwood Homes of Washington adopted this
system was for all of their homes in Year 3. One
potential consequence of using the hybrid system is increased
moisture in the belly; in Year 5, BAIHP staff will work
with Fleetwood plant staff to install data loggers in
several homes to determine whether this is a problem.
High
Efficiency Heat Pump Program: In order to be Energy
Star certified with a heat pump, the heat pump must meet
Energy Star specifications. BAIHP staff are in
the process of evaluating HSPF and SEER ratings for both
split and unitary systems. This evaluation involves
comparing reported manufacturer values with real-world
data from field-testing. Cost data investigations indicated
a $400 incremental cost for an Energy Star heat pump,
and coil sizing challenges when retaining the same “footprint”. Investigations
on new 90% efficient gas furnaces (Intertherm M3) will
take place in year 5.
Demonstration
Homes: Technical support was provided for the following
demonstration homes:
- WSU
Energy House: This 2600 ft.2 home has been
built to beyond SGC standards, and incorporates Energy
Star lighting and appliances. The home has received
significant national exposure through tours, an article
in the October 2000 issue of Automated Builder magazine,
a WSU campus and alumni newsletter, and the BAIHP website,
which includes house monitoring data. In addition,
BAIHP staff provided a tour to KING 5 News of Seattle,
which led to a television news item demonstrating Energy
Star Lighting and duct sealing. BAIHP staff use
the house to test additional innovative technologies
and testing methods. Working with Ecotope, ASHRAE,
and the Energy Conservancy, BAIHP staff conducted “Delta
Q” and “nulling” duct leakage tests
in Year 2. Follow up pressure tests and analysis
of test data conducted in Year 3 indicate that these
are effective methods of measuring duct leakage in manufactured
homes, and may be included in the upgrades to the NFPA
501 standards for manufactured homes.
Vincent
Village: Vincent Village is a 49 home rental
community, located in Richland, WA. All of
the homes are the same size, and in roughly the same
orientation. All of the homes are small, single
section, heated and cooled by Insider heat pumps. Half
the homes were built to SGC standards, the other
half were not. The development provides a unique
opportunity to compare the energy use of both SGC
versus non-SGC homes, and evaluate the long-term
performance of the Insider heat pump. Metered
utility data indicate average yearly savings
of $241 for the SGC homes.
-
Fish
Facility: Three SGC homes were built at the
Nez Perce tribal fish facility in Cle Elum, Washington. One
of these homes is equipped with Energy Star appliances
and lighting; all three homes are heated with Insider
heat pumps. Monitoring equipment was installed
in Year 2. In Year 3, preliminary blower
door testing indicated a high leakage rate. During
Year 4, tests found significant duct leakage due
to failure of butyl tape at risers on 2 year old
home. During Year 5, BAIHP staff and Fuqua
homes will make an effort to seal the ducts and
measure resulting improvements.
|