- Innovative Applications of Computer Technology on the Factory
Floor
UCF researchers continue to identify computer technology applications
for the modular factory floor. Research efforts during this
reporting period, focused on real time production labor data
collection. While labor represents a relatively modest fraction
of production cost, typically 10-15%, it has a profound impact
on operations, including product quality, cycle time, material
waste, and labor productivity.
Except for the slower winter months, experienced labor is
a scarce resource. Even if labor is sufficient in the aggregate,
it may not be positioned where it is most needed at a particular
moment in time. Competitive pressures are resulting in an
increasing mix of custom features, increasing the likelihood
of "floating bottlenecks" in production. Quality and safety
can suffer as undermanned crews rush to complete custom features
(i.e., fire-rated walls or a hip roof). If a crew cannot
keep pace, the line slows, production rate drops, overtime
is required, and delivery dates are missed.
In the past, the sheer number of production activities, lengthy
cycle times, and extensive product customization have discouraged
manufacturers from accurately estimating labor needs and using
this information to plan and control production. Instead
they have responded by controlling labor at the overall plant
level, attempting to maintain labor at a historical target
value stated as a percentage of overall production cost or
sales revenue. This approach seldom reflects the actual labor
content in the product, particularly during times of increasing
customization. To address the problem of shifting bottlenecks,
many manufacturers use flexible resources termed "utility
workers, flex workers, or expediters." However, the decision
to deploy these workers often is made with minimal planning,
after a problem has impacted the line.
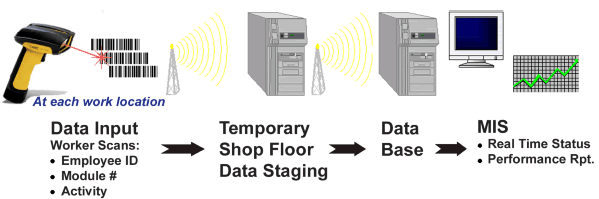 |
Figure
25. Schematic of the Status Tracking and Control
System (STACS). |
The Status Tracking and Control System (STACS) is a real time
labor data collection and reporting system. A schematic of
the STACS system is shown in Figure 25. Production workers
using wireless laser scanners, verify their current work assignment,
including employee number, module number, and activity number
with these scanners. The scanned information is transmitted
immediately to a base station and then to a local laptop,
where it is verified and temporarily staged. Information
is periodically transmitted via wireless LAN to a central
database computer where it is stored and used for reporting
purposes.
STACS reporting provides both real time manufacturing status
and summaries of historical production performance. Historical
results can be used for a variety of analytical and management
purposes:
- The development of analytical labor estimating models to estimate
labor requirements for product costing, production scheduling,
and labor planning.
- As a baseline for continuous improvement efforts.
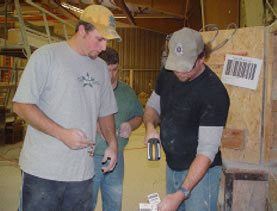 |
Figure 26. Testing alpha
prototype of STACS |
An alpha prototype of STACS was completed and tested at Avis
American Homes. (Please see Figure 26.) Test results in framing
and set indicated that manufacturing workers could operate
the system effectively and that the system accurately captured
scanned activity. (Please see Figure 27.) During the next
reporting period, researchers expect to test an enhanced version
of the system on a larger scale and develop labor models using
linear regression and neural nets.
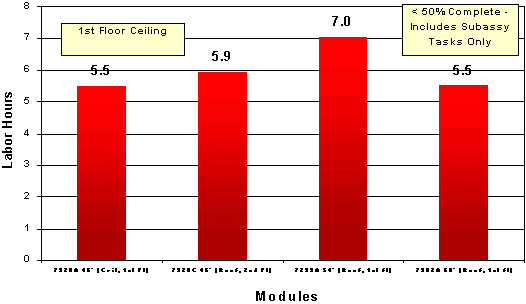 |
Figure
27. STACS alpha prototype results |
- Lean Production of Precast Concrete Panels
UCF researchers continued efforts to improve quality, reduce
costs, and increase energy efficiency as Arvida, a large Florida
builder, transitions from concrete block to precast concrete
panel construction. In 2002, UCF researchers completed a full
analysis of the precast panel operation and presented those
findings to management.
In 2003, value stream mapping identified activities that contributed
value to the customer and activities that added little or
no value. Material handling and rework were primary contributors
to the 47% of labor consumed by non-value added activities.
Once started, the flow of value-added activity was routinely
interrupted. Poor access to materials and tools, rework,
ill-defined process flows, and workforce/first line supervision
issues were contributing factors to work flow interruptions.
To address these issues, UCF researchers utilized lean production
principles - challenging non-value added activities and removing
the obstacles to continuous production flow. Researcher recommendations
addressed organization/communication, structured procedures
and continuous work flow, material handling, and off-line
sub-assembly issues. (Please see Figure 28.)
Preliminary estimates indicate that labor may be reduced as
much as 60% and cycle time by 25% if these recommendations
are implemented. The research team plans a full-scale operating
test of the recommendations in Year 5. If these recommendations
are accepted, researchers will assist Arvida and their primary
contractor, Trinity, in detailing the design of the insulated
panel walls and in the design of a new precast plant to serve
the north Florida market.
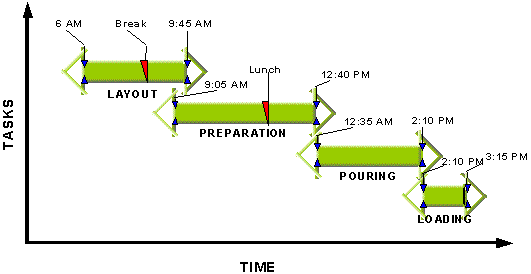 |
Figure
28. Summary of typical daily production schedule
using continuous flow. |
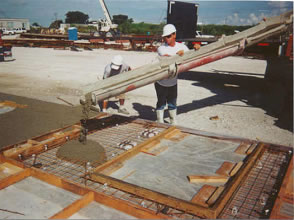 |
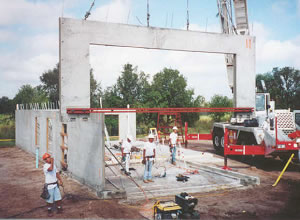 |
Figure
29. Pouring precast panels. |
Figure
30. Setting precast panels. |
UCF researchers are currently collaborating with FSEC colleagues
to develop an order of magnitude energy savings in modular
housing and to develop insulation strategies for precast concrete
walls for the north Florida market. (Please see Figures 29
and 30.) Trinity currently uses no wall insulation in their
concrete walls for central and south Florida.
|