|
|
|
Reference
Publication:
Chandra, Subrato, Neil Moyer, Danny Parker, David Beal,
David Chasar, Eric Martin, Janet McIlvaine, Ross McCluney,
Andrew Gordon, Mike Lubliner, Mike McSorley, Ken Fonorow,
Mike Mullens, Mark McGinley, Stephanie Hutchinson, David
Hoak, and Linda Tozer. Building America Industrialized
Housing Partnership, Annual Report - Fourth Budget Period.
04/01/03-03/31/04. |
|
|
Building
America Industrialized Housing Partnership, Annual
Report - Fourth Budget Period |
|
|
Subrato
Chandra, Neil
Moyer, Danny
Parker, David
Beal, David
Chasar, Eric
Martin, Janet
McIlvaine, Ross
McCluney, Andrew
Gordon, Mike
Lubliner, Mike McSorley, Ken
Fonorow, Mike
Mullens, Mark
McGinley, Stephanie
Hutchinson, David
Hoak, and Linda Tozer |
|
Florida
Solar Energy Center |
|
|
|
Avis
American Homes: Researchers from the UCF Housing Constructability Lab are
assisting Avis American Homes in the design of a modular production
facility expansion for their plant in Avis, Pennsylvania.
Avis is a division of Excel Homes, one of the largest modular
producers in the US. This facility expansion is expected
to boost Avis plant capacity by about 50%.
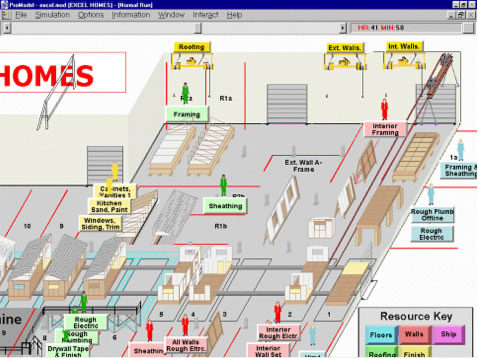 |
Figure 23. Factory simulation
model of new modular factory: Framing
|
Researchers have provided technical assistance in the new
facility design by helping Avis incorporate lean manufacturing
principles, making the new factory more flexible, responsive,
and efficient. To test these lean manufacturing concepts,
researchers developed a computer simulation model of the proposed
new factory. An example of a similar model is shown in Figure
23 above.
The expanded plant, which will use a shotgun production layout,
will have the distinction of being the highest capacity modular
plant in the US. This layout concept incorporates two adjacent
parallel production lines, with modules flowing lengthwise
along each line. Each line will be supplied by its own dedicated
sub-assembly stations (i.e., floors, walls, and roofs). Most
finish activities will be performed by teams of workers that
alternately serve both lines.
The shotgun layout has several important advantages. With
two lines, the cycle time on each line is twice as long and
results in half as many moves and production interruptions.
Lengthwise module orientation boosts production efficiency
because large, bulky exterior building materials used on the
walls and roof (i.e., insulation, sheathing, shingles, siding)
can be staged closer to the point of use. Also permanent
mezzanines allow roof access and rid the facility of catwalks
that must be raised and lowered during each line move. However,
the shotgun layout does create some unique design challenges.
The crane system that moves the primary sub-assemblies to
each line must accommodate the desired independence of each
line. Accessing interior building materials (i.e., cabinets
and trim) also can be more difficult with the shotgun approach.
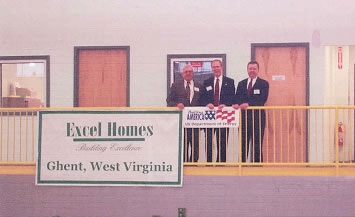 |
Figure
24. Grand Opening of
new Excel Modular Plant |
Excel
Homes: In January 2002,
researchers from the UCF Housing Constructability Lab participated
in the grand opening of Excel Homes' new modular production
facility in Ghent, West Virginia. (Please see Figure 24.)
Excel Homes is one of the largest modular producers in the US.
This new factory increased their production capacity about 50%.
UCF researchers also provided Excel with technical assistance
in their new operation design, incorporating similar lean manufacturing
principles recommended to Avis homes. To
test recommended concepts, researchers developed a computer
simulation model of the proposed new factory. The model was
developed using a previous Building America research product,
the Generic Modular Manufacturing Simulation System (GMMSS).
GMMSS allowed researchers to create a realistic model of the
complex, high-volume factory in a relatively short time.
As a result, several major improvements were incorporated
into the factory design.
- Supersize drywall was used for interior ceiling and wall applications,
reducing the number of drywall sheets handled and minimizing
drywall seams.
- Industrial manipulators and mechanized material bridges facilitated
supersize material handling.
- Replacing mechanical fasteners (drywall screws) with foam
adhesive further reduced the drywall finishing effort by
eliminating holes.
- Additional cranes were added to facilitate the flow of framed
subassemblies to the line.
- Pairwise line movement practices were instituted, effectively
reducing line disruption during moves by 50%.
- Roofing (sheathing and shingling) and ceiling drywall activities
were moved off-line, allowing drywall activities to be performed
at the same time roofing activities are being performed
at the floor level. This reduced production cycle time
and enhanced safety.
- Customization bays were added to allow more extensive, value-added
customization without degrading line movement.
|
Disclaimer:
This report was prepared as an account of work sponsored by an agency
of the United States government. Neither the United States government
nor any agency thereof, nor any of their employees, makes any
warranty, express or implied, or assumes any legal liability
or responsibility for the accuracy, completeness, or usefulness
of any information, apparatus, product, or process disclosed,
or represents that its use would not infringe privately owned
rights. Reference herein to any specific commercial product,
process, or service by trade name, trademark, manufacturer,
or otherwise does not necessarily constitute or imply its endorsement,
recommendation, or favoring by the United States government
or any agency thereof. The views and opinions of authors expressed
herein do not necessarily state or reflect those of the United
States government or any agency thereof.
|