|
|
|
Reference
Publication:
Chandra, Subrato, Neil Moyer, Danny Parker, David Beal,
David Chasar, Eric Martin, Janet McIlvaine, Ross McCluney,
Andrew Gordon, Mike Lubliner, Mike McSorley, Ken Fonorow,
Mike Mullens, Mark McGinley, Stephanie Hutchinson, David
Hoak, and Linda Tozer. Building America Industrialized
Housing Partnership, Annual Report - Fourth Budget Period.
04/01/03-03/31/04. |
|
|
Building
America Industrialized Housing Partnership, Annual
Report - Fourth Budget Period |
|
|
Subrato
Chandra, Neil
Moyer, Danny
Parker, David
Beal, David
Chasar, Eric
Martin, Janet
McIlvaine, Ross
McCluney, Andrew
Gordon, Mike
Lubliner, Mike McSorley, Ken
Fonorow, Mike
Mullens, Mark
McGinley, Stephanie
Hutchinson, David
Hoak, and Linda Tozer |
|
Florida
Solar Energy Center |
|
|
|
By 2002, all 20 northwest manufacturers had signed Energy
Star partnership agreements. In 2003, BAIHP staff recruited,
Flexible Technologies, RADCO, and Friedrich as Energy Star
industry partners.
-
High Efficiency Heat Pump Program
To be Energy Star certified with a heat pump, the heat pump
must meet the program specifications. Cost data investigations
indicate a $400 incremental cost for an Energy Star heat
pump, and coil sizing challenges when retaining the same
"footprint." Similar evaluations on 90% efficient gas
furnaces (Intertherm M3) will take place in the next reporting
period. BAIHP staff now are in the process of evaluating
HSPF and SEER ratings for both split and unitary systems
to see how reported manufacturer values compare with real
world field-collected data.
BAIHP staff visits each of the manufactured housing plants
quarterly to verify compliance with SGC/NC/E-Star specifications.
Inspections include a plant audit, ventilation system testing,
and construction-related troubleshooting with plant staff
and independent inspectors. Persistent plant issues include
lack of attention to duct installation and sealing, and
improper wall insulation sizing which results in installation
compression or voids. (Please see Figure 16.)
In December 2002, BAIHP staff conducted a quarterly in-plant
inspection at Valley Manufactured Housing in the company
of local utilities, DOE, BPA, and PNNL personnel, with the
goal of fostering closer ties between the manufactured home
industry, regulating agencies, and utilities.
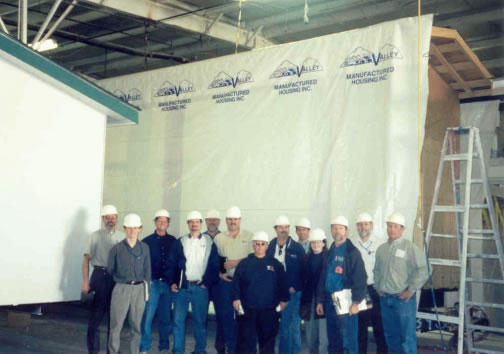 |
Figure 16. Quarterly plant
inspection in the company of representatives from utilities,
DOE, BPA and PNNL at Valley Manufactured Housing in
Sunnyside Washington. |
Refinement of SGC/NC Standards:
BAIHP staff have been working to refine existing SGC/NC specifications,
in large part to incorporate innovative building technologies
researched by BAIHP. As part of the specification revision,
BAIHP staff have collaborated with EPA and other regional
partners to clarify the equivalency of SGC/NC with Energy
Star. This year, BAIHP staff developed a new Energy Star
compliance path for climate zone 2 that doesn't require a
heat pump. The non-heat pump path uses a heat recovery ventilation
system, a .93 EF water heater, and a tighter duct and envelope
system.
-
New Product and Technology Evaluation
Energy
Conservancy: BAIHP
staff worked with the Energy Conservancy to evaluate their
new products for measuring air handler and exhaust fan flows.
Fireplace
Controls: A 12-volt
DC battery backup, charging, and inverter system was installed
in the WSU Energy house to operate the propane fireplace
during power outages. Tests revealed that the backup system
operates the propane fireplace for up to 48 hours during
a power outage, while maintaining comfortable indoor temperatures
even during severe winter conditions. BAIHP staff have
discussed this concept with HVAC and fireplace industry
partners as a potential disaster preparedness option.
Integrated
Control of Heat Pump and Gas Fireplace Controls
:
Discussions are underway with the HVAC industry and utility
partners to integrate heat pump and fireplace controls in
the WSU Energy House. This would allow the thermostat to
turn on either the fireplace or the heat pump's electric
resistance heat strips when the heat pump cannot meet the
home heating loads. This allows load shifting benefits
for utilities and their customers during the winter peak
and provides a good marketing strategy for HVAC manufacturers
who sell both gas fireplaces and heat pumps to the manufactured
housing industry.
Flexible
Technologies: BAIHP
partner Flexible Technologies developed an innovative system
that improves the heat and tear resistance of the duct inner
liner, reduces ductwork crimping without using sheet metal
elbows, and improves the system-to-air seal where the crossover
duct penetrates the bottom board. BAIHP and Flexible Technologies
staff have been working with the region's manufacturers
to promote the use of this new system.
Insider
Heat Pump: Monitoring
of the Insider heat pump at the WSU Energy House began in
2000. The measured flow rate of the indoor unit was good
(850 CFM total, 425 CFM per ton), but BAIHP staff identified
two performance issues: a too-frequent operation of the
defrost cycle, and a lower than expected airflow at the
outdoor coil. Continued testing of the Insider in 2001,
indicated a 10% increase in coefficient of performance (COP)
due to increased airflow at the outdoor coil. In 2002,
WSU staff worked with FSEC to analyze performance data on
the Insider heat pump.
At Vincent Village, the property manager indicated a high
degree of satisfaction with the Insider heat pumps, with
no comfort complaints since 1996. One Insider has been
replaced and minor maintenance has been required to unclog
some condensate drains.
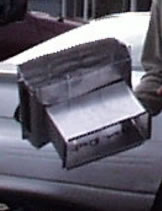 |
Figure
17. Duct riser developed by BAIHP partner LaSalle. |
La
Salle Duct Riser: BAIHP
staff worked with BAIHP partner La Salle Air to design and
produce a duct riser for manufactured homes that uses mastic
instead of tape. (Please see Figure 17.) BAIHP staff demonstrated
prototype designs of the riser to Northwest manufacturers
in 2002. Three manufacturers, Redman, Fleetwood, and Marlette,
have adopted the new riser; and several others are considering
it. BAIHP staff also have worked with Fleetwood's national
office to promote the use of the riser in all Fleetwood
plants.
In offering technical support to owners of over 100,000 homes
built since 1990, staff answer questions from homeowners,
manufacturers, retailers, and others. From late 2002 to
mid-2003, staff from Washington, Oregon, and Idaho responded
to over 70 phone calls and conducted 15 field visits. The
number of problem home field visits has significantly decreased
over the history of the program, due in large part to increased
manufacturer and installer awareness of the SGC/NC/E-Star
specifications. Also, Washington and Oregon now require
manufactured home installer certification.
To support the certification process, BAIHP staff participates
in quarterly meetings of the Washington State Manufactured
Housing Technical Working Group. This group coordinates
the certification of manufactured housing set-up crews.
In 2001, 50 set-up crew received the training. During 2002,
exactly 100 set-up crew personnel attended training and
were certified.
A consistent field issue for manufactured homes continues
to be excessive duct leakage, mostly because of butyl duct
tape failure. (Please see Figures 18 and 19.) These findings
were brought to the attention of the NFPA-501 Manufactured
Housing Standards Committee, resulting in a successful proposal
to revise the duct sealing specifications in the NFPA-501
Standard.
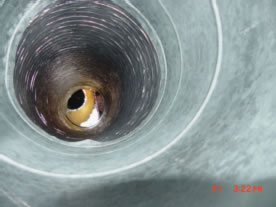 |
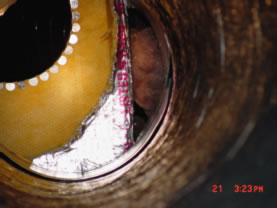 |
Figure 18.
Riser disconnect |
Figure 19. Riser
disconnect close-up. |
By early 2003, additional manufacturers eliminated the use
of butyl tape for duct sealing, and began using mastic sealing
instead. Fleetwood Homes of Washington, Marlette, Palm
Harbor Homes, and Guerdon all adopted mastic. In-plant
testing indicates significant improvement in the duct leakage
rates of these homes. During the next reporting period,
BAIHP staff will continue to test duct leakage rates both
in the plant and in the field.
In 2000, staff in Idaho and Washington field-tested 49 SGC/NC
homes built from 1997 to 1998. In 2001, analysis of field
test data confirmed some improvements to home setup procedures
and air leakage control, while highlighting a need to improve
duct tightness and ventilation system operation (through
homeowner education). In early 2002, BAIHP staff produced
an updated homeowner ventilation brochure. Following this,
BAIHP staff worked with Ecotope to develop a valid sample
for the next round of field testing, and began to develop
the test protocol. Currently, field testing is scheduled
for the summer of 2003.
|
Disclaimer:
This report was prepared as an account of work sponsored by an agency
of the United States government. Neither the United States government
nor any agency thereof, nor any of their employees, makes any
warranty, express or implied, or assumes any legal liability
or responsibility for the accuracy, completeness, or usefulness
of any information, apparatus, product, or process disclosed,
or represents that its use would not infringe privately owned
rights. Reference herein to any specific commercial product,
process, or service by trade name, trademark, manufacturer,
or otherwise does not necessarily constitute or imply its endorsement,
recommendation, or favoring by the United States government
or any agency thereof. The views and opinions of authors expressed
herein do not necessarily state or reflect those of the United
States government or any agency thereof.
|