Presented
at the “NAHB International Builders Show,” conference
sponsored by National Association of Home Builders, Las Vegas,
NV, January 2003.
Lean Homebuilding using Modular Technology
Michael A. Mullens, Ph.D., PE
Department of Industrial Engineering & Management Systems
University of Central Florida
Orlando, FL 32816-2450
Mark E. Kelley, III
Building Science Engineering
85 Depot Road
Harvard, MA 01451
Abstract
This paper describes an effort to apply the principles
of lean production to modular homebuilding. To organize the
effort, a kaizen blitz was used in a brief, but intense
attack on construction waste and inefficiency. Several
factors made this effort unique. First, the homebuilder
used factory-built modules, which suggested that the improvement
team must be extended up the supply chain to include both
the modular manufacturer and builder and down the supply
chain to include sub-contractors. Second, conventional
concepts of continuous flow and batch production were extended
to a project oriented construction environment. This paper
describes how these issues were resolved and presents actual
results. Results included substantial reductions in construction
cycle time and significant improvements in safety, quality,
productivity and energy efficiency.
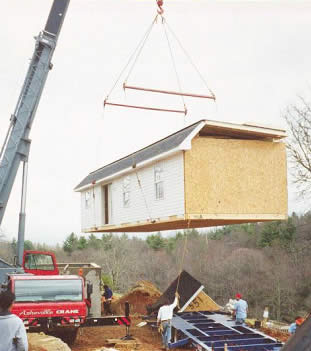 |
Figure
1. Setting a typical module. |
1. Introduction
Modular construction is a promising new industrialized homebuilding
technology that uses large, factory-produced modules (Figure
1) to construct homes (Figures 2 & 3). The approach
differs from conventional stick-built construction, which
uses smaller, elemental building components that are fabricated
and assembled on the construction site. The primary advantage
of modular construction is that most production operations
are performed in the factory, allowing the builder/manufacturer
to control the building environment and take advantage
of modern manufacturing processes. Ideally, modular construction
should produce a higher quality home delivered to the customer
faster at lower cost.
Not
all modular homebuilding processes can be moved inside
the factory. Modules must still be set on the foundation,
joined structurally and made watertight. Site-built structures
such as garages and decks must be added. Utilities must be
connected between modules and with the main service. HVAC
systems must be installed. Local inspectors must ensure code
compliance. Interior and exterior marriage joints must be
finished. These on-site processes are often thought (and
marketed) to be much simpler than conventional stick building.
The reality, however, is that these operations are not trivial
and can be a source of quality problems, delivery delays,
and cost overruns.
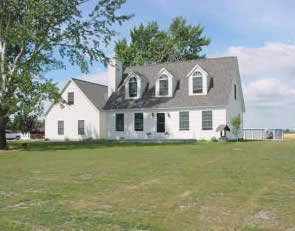 |
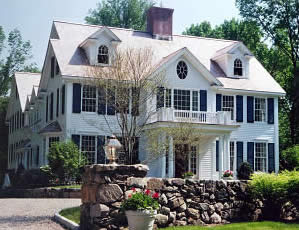 |
Figure
2. Typical modular cape home. |
Figure
3. Large modular custom home. |
To
address these challenges, a multi-disciplinary group of
housing researchers is leading an effort to apply lean
production principles to on-site finish operations. The
objective of lean production is simple: to use less of
everything to design and produce products economically
at lower volumes with fewer errors [1]. Five principles
have been recognized as fundamental to lean production
[1]. These principles and their implications for modular
homebuilders are summarized below.
- Identify
what the customer values – modular homebuilders
must give their customers flexibility, providing a
rich product mix and allowing homebuyers to customize
their homes.
- Identify
the value stream (the steps necessary to create value
for the customer) and challenge all wasted steps – modular
homebuilders have taken an important first step to
reduce waste, reconfiguring their supply chains by
turning to large Tier 2 suppliers (module manufacturers).
These modular manufacturers, in turn, use lean production
techniques in their factories to reduce waste and maximize
value to the homebuilder. When modules are delivered
to the construction site, modular homebuilders must continue
to challenge all waste including scrapped materials,
delays, rework, and excess labor.
- Produce
the product when the customer wants it and, once started,
keep the product flowing continuously through the value
stream – this
is difficult for modular homebuilders, and even more
so for conventional builders. Builders typically rely
heavily on independent sub-contractors and building
inspectors. To maintain continuous flow, homebuilders
must develop partnerships with reliable and flexible
subs, accurately schedule activities, and strive to maintain
the overall building schedule.
- Introduce
pull between all steps where continuous flow is impossible – modular
homebuilders must pull subs and inspectors onto the
job site when they are needed. Because subs and inspectors
cannot build inventory by producing in advance, scheduling
is important to minimize scheduling conflicts and their
resulting delays.
- Manage
toward perfection – modular
homebuilders must continuously assess their performance,
adjust strategies and improve.
To
apply these lean production principles, the research group
organized and led a kaizen blitz. Kaizen can be defined
as “the planned, organized and systematic process of
on-going, incremental and company-wide change of existing
practices aimed at improving company performance” [2].
In contrast to scientific management approaches that split
employees into ‘thinkers’ and ‘doers’,
kaizen assumes that all employees can make a contribution
to problem solving and innovation [3]. The kaizen blitz takes
the same improvement philosophy and applies it in a brief,
but intense attack on production waste and inefficiency [4].
Both the continuous and blitz forms of kaizen are key elements
of lean manufacturing and six sigma production systems [5].
A high quality, high volume modular builder (80-100 homes
per year) agreed to serve as the test bed for the effort.
This paper describes the approach used, actual results, recommendations,
conclusions and future research directions.
2. The Kaizen Blitz Approach
The kaizen blitz was accomplished in three phases, pre-blitz
planning, blitz and blitz follow-up.
2.1 Pre-blitz Planning
To prepare for the kaizen blitz, key players met four weeks
prior to the event. Participants included the president
and project manager from the homebuilder, an engineer from
the modular manufacturer, a lean consultant and a housing
researcher. The team agreed upon objectives (Table 1),
scope, and the preliminary schedule. To focus the effort,
project scope was limited to finish activities occurring
after the modules are set, the roof is raised and the home
is made watertight. These first three activities are typically
completed in 1-2 days and are generally considered highly
efficient. Dates were finalized. The consultant also led
the group in a review of lean production concepts, focusing
on the value stream, waste (or muda) and single piece,
continuous flow.
Benchmark |
Units |
Target |
Productivity |
Hr./sq.ft. |
Increase
20% |
Quality |
Repair
hr./sq.ft. |
Decrease
50% |
Cycle
time |
Days |
Decrease
50% |
Energy |
BTU/sq.ft. |
Decrease
50% |
Table
1. Kaizen blitz objectives.
2.2 The Kaizen Blitz
The kaizen blitz took place during the week of August
6-10, 2001, in the builder’s headquarters and on various
construction sites. Full time participants included the builder’s
president and project manager, the modular manufacturer’s
production manager and production engineer, the consultant,
and three housing researchers.
The
first two days were spent on one construction site observing
early finish activities for a four-module colonial home.
The team initially focused on quality issues, since discrepancies
from manufacturing, shipping and set must be identified and
repaired before true value-adding activities can begin. Based
on observations and discussions with the builder’s
construction crew, the team developed a list of common quality
problems, estimated average repair times and identified likely
root causes. Average repair time totaled about 64 man-hours
per home. The majority (78%) of these repairs were attributed
to transport. Racking and motion caused a large number of
drywall cracks as well as nail pops and repainting needs.
The factory was responsible for some defects in cabinetry,
electrical, window alignment and drywall taping. Factory
representatives on the team indicated that most of the manufacturing
discrepancies and shipping damage could be avoided by changing
factory processes and agreed to follow-up. They also suggested
that the builder switch to a faster drying drywall compound
to reduce drying time after each of the three coats. Other
recommended quality improvements included using metal grates
at home entry to reduce dirt tracked inside, changing flashing
detail on exterior doors, letting in the dado on all exterior
walls, and putting dye in drywall compound for visual detection.
A critical element of home quality is the energy performance
of the home, which impacts indoor air quality, comfort and
energy costs. The team identified a number of opportunities
including uninsulated areas, ineffective gaskets and air
barriers, and poor procedures for air sealing at module connections
and windows. Recommendations included: 1) insulate the foundation
walls rather than the ceiling above the basement, 2) double
seal marriage joints with gaskets and foam, with the gasket
serving as a backer for the foam, 3) have the factory caulk
the electrical outlets and light switches or install a sealed
and gasketed box, 4) have the factory seal around the window
with foam instead of fiberglass, 5) have the factory install
bath and kitchen fans with higher quality dampers to prevent
air infiltration, and 6) change band joist insulation to
better fill cavities. These changes are expected to cut energy
costs by over 40%.
The team discovered several opportunities to improve safety
on the construction site, including the use of portable stairs
to enter the home (instead of a board), the immediate removal
of ship-loose siding to eliminate a tripping hazard, and
the use of temporary covers to cover open bulkheads.
The team observed numerous opportunities for improving supervision
on the construction site. Workers arrived on site at 7:30
AM, but no drywall work could begin until materials arrived.
Daily set-up and tear-down time for carpenters was substantial.
Since there were no bathroom facilities or coffee on site,
workers left the site for breaks, typically taking more than
45 minutes for each break. Productivity was further reduced
by a delay in electrical service. In summary, the team agreed
that the project manager should focus on 1) planning and
supervising the work so that the right resources (workers,
materials, tools, utilities) are available when needed and
2) keeping the workers on the job and working efficiently.
More specifically, the team recommended that a Porta-Potty,
dumpster, generator and job box be placed on each jobsite.
Also apparent were inefficiencies related to ship-loose
materials. Stacks of material were moved repeatedly (up to
12 times) to access one wall and then another. Lost time
is estimated at over 2 man-hours. Stepping over the materials
created a safety hazard. During the kaizen, the builder and
manufacturer agreed on optimal placement of shiploose materials.
For example, the manufacturer agreed to place electrical
fixtures in the closet closest to the kitchen.
On
the third and fourth days of the kaizen blitz, team members
moved into the builder’s office. Here they estimated
labor requirements and developed scenarios for continuous
flow. The average value-added labor (man-hours) required
to complete each activity was estimated by the builder’s
project manager and refined by team members. These labor
estimates were then allocated to the builder’s six-person
construction crew, subcontractors and inspectors based on
current practices. A summary of the results for the builder’s
crew is shown in Figure 4. Several points should be noted.
First, each crewmember is assigned a variety of tasks, both
within and outside of his/her trade, based on previous experience
and skills. Second, there is a large variance in the labor
hours assigned to each crewmember. This suggests that crewmembers
with shorter assignments will be idle as they wait for those
with longer assignments. Third, the TAKT time (or demand
cycle) was calculated using peak summer sales as shown in
Equation 1.
TAKT time = 65 working days / (15 homes / 2 crews) = 8.6
working days / home/ crew (1)
In other words, each crew must complete an average of one
home every 8.6 working days (68.8 hours) in order to meet
average customer demand. This is dramatically less than 13
week (65 working day) delivery time currently promised by
the builder, indicating a substantial opportunity to reduce
cycle time and related waste. Fourth, optimal construction
crew size can be calculated as shown in Equation 2.
Construction crew size = 208 total crew labor hours per
house/68.8 clock hours per house (2)
= 3 crew members
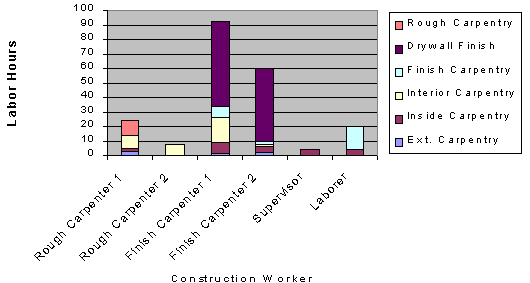
Figure 4. Average value-added labor per
home by crewmember (builder employees only)
The
optimal 3-person crew size is significantly less than
the current 5-person crew (plus the supervisor) and is
based on several key assumptions: 1) the non-value added
activities discussed earlier have been completely eliminated
and 2) crew members are sufficiently cross-trained to equally
balance the workload.
Much
of the waste in the finish process can be attributed to
the batch construction scheduling strategy (Figure 5) employed
by the builder. The builder uses two 5-person construction
crews. Each crew has up to eight homes under construction
at the same time. The builder promises customers that their
homes will be completed within 13 weeks (65 working days)
from module set. The builder routinely delivers within several
days of the promised delivery date. Note that the home is
idle for most of the 13 week construction cycle. This clearly
violates the third principle of lean production – keep
the product flowing through the value stream. In the context
of finishing the modular home, this principle suggests single
home flow - starting and completing one house at a time (Figure
6). This impacts both cycle time and productivity. Using
single home flow, far less time will be spent traveling between
multiple construction sites and setting-up/tearing-down equipment.
No longer will construction inefficiencies be masked by moving
the crew to another home, creating travel-related inefficiencies.
For example, a delay caused by an electrical subcontractor
not completing the rough-in is masked by the carpenters (who
cannot finish the drywall until the wiring is completed)
moving to another site. Single home flow exposes problems
so that they can be addressed immediately. The extended cycle
time resulting from batch construction also permits other
problems to develop. Customers may simply change their minds,
damage can occur and the home must be cleaned.
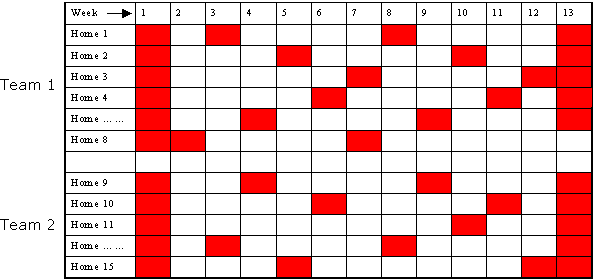
Figure 5. Current batch construction scheduling strategy.
The
team next developed a construction plan using MS PROJECT,
assuming single home flow. Potential precedence relationships
were identified and process times were estimated, assuming
no non-value added tasks and a crew size of three. Subcontractors
and building inspectors were included in the plan, using
conservative estimates for their response times. A critical
path analysis of the construction plan indicated that a
typical home could be completed in about 10 working days.
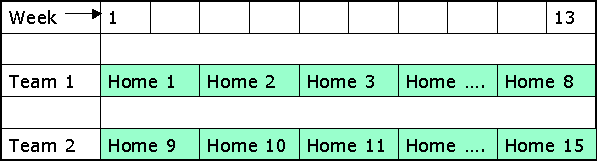
Figure 6. Single home construction approach recommended by
the team.
On
the final day of the kaizen blitz, the team summarized
and presented findings and recommendations to the builder’s
staff. Using staff feedback, the team agreed to add another
week to the cycle time to reflect delays inherent in the
construction process (i.e., weather, building inspectors).
After discussion, the builder committed to making most of
the recommended changes.
2.3 Blitz Follow-up
In October 2001, reporting to a group of modular manufacturing
executives, the president of the builder reported that
they were making considerable progress and many new policies
and scheduling changes had been applied. He noted that
although they have only begun the process, they have already
reduced cycle times from 13 weeks to 8 weeks per house.
This progress was made by reducing some of the waste identified
during the kaizen and by tighter scheduling. The builder
did not attempt single home flow, citing a lack of confidence
in the details of the recommended construction plan and
in the willingness of subcontractors to comply. The builder
also indicated that they were distracted by an increase
in sales and the need to bring on a second module supplier
due to excessive lead times.
Researchers
conducted a 2-day follow-up visit to the builder in August
2002. The objective was to restart the builder’s
improvement process. The primary focus was the development
of a more realistic construction plan, incorporating additional
detail and refining precedence relationships between activities.
In addition to the original participants, subcontractors
were invited - to introduce them to the concept of single
home flow and to gauge their commitment. Several key subs
attended and all expressed a willingness to maintain a tight
construction schedule, with sufficient advance notice. The
resulting construction plan (Figure 7) yields a construction
cycle of about 30 work days during the winter and about 20
days during the remainder of the year. During the cold winter
months, the builder requires the heating system to be operational
before finishing the drywall. The builder also decided to
organize around a 4- person crew, the minimum considered
practical. Note that all red tasks in the plan are on the
critical path. The remaining blue tasks are non-critical
with slack times shown to the right of the bars. Slack times
indicate how long the task can be delayed without impacting
the overall schedule.
3. Conclusions and Future Research
Modular homebuilders can apply the principles of lean production
to achieve substantial improvements in safety, quality,
cycle time, construction costs and energy performance.
Transitioning from multi-home batch construction to single
home flow is believed to be particularly important, since
it is essential to cycle time reduction and related quality/cost
improvements.
Future research is likely to focus on several areas. First,
the authors hope to continue to work with the builder, particularly
in the area of subcontractor partnering. Electricians and
plumbers are notoriously independent. Therefore their cooperation
will be essential in achieving single home flow. Second,
the lessons learned in this exercise must be documented and
transferred to other builders through a training program.
It is imperative that gains are consolidated and that energy
efficiency improvements are closely coupled with any transfer
of this technology to other builders.
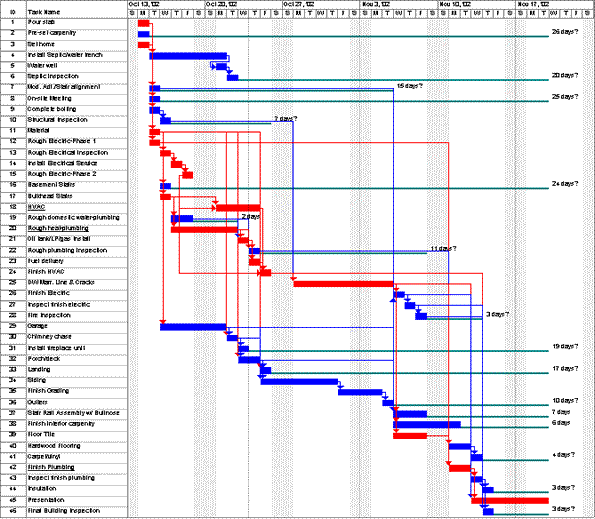
Acknowledgements
The authors wish to thank the U.S. Department of Energy,
Office of Building Technology, State and Community Programs
for their support in funding the UCF Housing Constructability
Lab [6] and the Hickory Consortium [7] to perform this
housing research through the Building America [8] program.
This support does not constitute an endorsement by DOE
of the views expressed in this report. The authors appreciate
the encouragement and support from George James, program
manager in Washington DC.
References
1. Womack, J. and Jones, D., 1996, Lean Thinking : Banish
Waste and Create Wealth in Your Corporation, Simon & Schuster,
New York.
2. Boer, H., Berger, A., Chapman, R. and Gertsen, F. (Eds.),
2000, CI Changes: from Suggestion Box to Organizational Learning – Continuous
Improvement in Europe and Australia, Ashgate, Aldershot.
3. Bessant, J., Caffyn, S., and Gallagher, M., 2001, “An
Evolutionary Model of Continuous Improvement Behaviour,” Technovation,
21, 67-77.
4. Laraia, A., Moody, P., Hall, R., 1999, The Kaizen
Blitz: Accelerating Breakthroughs in Productivity and Performance,
Jossey-Bass, San Francisco.
5. Pande, P., Neuman, R., and Cavanagh, R., 2000, The
Six Sigma Way : How GE, Motorola, and Other Top Companies
are Honing Their Performance, McGraw-Hill, New York.
6. http://hcl.engr.ucf.edu/
7. http://www.hickoryconsortium.org/
8. http://www.eren.doe.gov/buildings/building_america/
|