Disclaimer: This
report was prepared as an account of work sponsored by an agency
of the United States government. Neither the United States government,
nor any agency thereof, nor any of their employees, makes any warranty,
express or implied, or assumes any legal liability or responsibility
for the accuracy completeness, or usefulness of any information,
apparatus, product, or process disclosed, or represents that its
use would not infringe privately owned rights. Reference herein to
any specific commercial product, process, or service by trade name,
trademark, manufacturer, or otherwise does not necessarily constitute
or imply its endorsement, recommendation, or favoring by the United
States government or any agency thereof. The views and opinions of
authors expressed herein do not necessarily state or reflect those
of the United States government or any agencies thereof.
II.
BAIHP Technical Assistance HFH
Habitat for Humanity-BAIHP
Partnership
Americus, Georgia (HFHI) and Habitat affiliates nationwide
Category A, 11 Homes (Lakeland HFH)
Category B, 446 Homes
Category C, 260 Homes
Papers: Case
Study: 2003 Jimmy Carter Work Project, LaGrange Site
Case
Study: Florida Habitat Homes in Lakeland, Broward and Alachua Counties
Case Study: Houston Habitat for Humanity
Beal, David and Janet McIlvaine (2006.) “Energy and Indoor
Air Quality Recommendations for Cold Climate Habitat for Humanity Homes.” FSEC-CR-1647-06,
Florida Solar Energy Center, Cocoa, Florida. August 2006.
The Building America-Habitat for Humanity partnership, formed in 1995
at Habitat’s Environmental Initiative Kickoff, has brought BAIHP
into the design, construction, and evaluation process of over 600 Habitat
homes across the nation built by 50 Habitat for Humanity affiliates in
more than 20 states. BAIHP activities with Habitat (including those conducted
under the Energy Efficient Industrialized Housing Project) are listed
in Table 19 (page 61). Activities generally fall into three
categories:
-
Technical Assistance to Habitat for Humanity International (HFHI),
high profile HFHI projects (Congress Building America, Builders Blitz,
and Katrina Recovery, and HFH affiliates (local chapters)
-
Research
-
Training at regional and national HFH conferences
Introduction:
BAIHP energy efficiency recommendations for Habitat
homes all meet the following four criteria in increase likelihood of
sustainable change and to ensure a good fit with Habitat's construction
process and business model:
-
Proven reliable and cost effective
-
Volunteer friendly
-
Readily available in current market
-
Easily maintained and repaired by normal trades
Since the inception of FSEC’s partnership with Habitat, researchers
have been privileged to work along side some of America’s brightest
building scientists representing SouthFace Energy Institute, Oak Ridge
National Laboratory, National Renewable Energy Laboratory, contractors
with the California Energy Commission, the Alliance to Save Energy, various
electric and multi-fuel utilities, members of Habitat’s own Green
Team (defunct in 2004), and volunteer members of the Energy Efficient
Building Association. In 2005, BAIHP and Habitat partnered with RESNET
to team volunteer Home Energy Raters with Habitat affiliates in HFHI’s
Congress Building America Program (more information on this project below),
expanding that partnership in 2006 to include all interested Habitat
affiliates.
Partially because of Building America (and other DOE supported organizations)
involvement with Habitat over the past 10 years, HFHI adopted Energy
Star as one of their two Best Construction Practices for all U.S. affiliates.
Best Practices are used to evaluate affiliate status. This represents
a major commitment to energy efficiency from the highest ranks of Habitat
International. Affiliates are encouraged to consistently achieve Best
Practices and the requests for and prevalence of Energy Star ratings
for Habitat affiliates has surged as a result.
I. A. Technical Assistance to Habitat for Humanity International
(HFHI),
high profile HFHI projects (Congress Building America, Builders Blitz,
and Katrina Recovery, and HFH affiliates (local chapters)
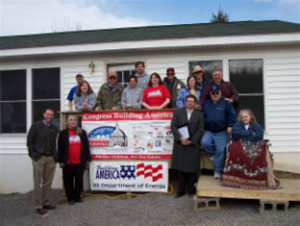 |
Figure 24. Almost Heaven
Habitat for Humanity’ Congress Building America house on
day of dedication. |
Congress Build America (CBA) (February 2005 – June 2006)
Background:
In February of 2005,BAIHP researchers announced
DOE’s Building America partnership with Habitat for Humanity
International’s (HFHI) Congress Building America (CBA) project.
The announcement was made at the dedication of Almost Heaven’s
CBA house (Figure 24) which was built in partnership with
Shelley Moore Capito, United States Representative second congressional
district of West Virginia. Identical concurrent resolutions--Senate
Concurrent Resolution 43 and House Concurrent Resolution 184 express
the Congressional support of this project.
The memorandum of understanding between the affiliates and the HFHI
includes language making the Building America technical review part of
the standard process. All CBA affiliates were invited to submit designs
to BAIHP researchers for evaluation. Researchers expected to conduct
about 30 evaluations based on an expected response of 30% of the projected
100 houses to be built under the program.
Actual construction of CBA houses fell dramatically short of this 100
house expectation due to a nationwide re-direction of effort to support
the Gulf Coast Recovery (see next section for more info) and to participate
in another HFHI program called the Builders Blitz.
CBA-BA Partnership Kick Off:
After announcing the CBA-BA partnership
formally in West Virginia at the dedication of the first WV CBA house
(February 2005), researchers attended HFHI’s Urban Conference in
Washington D.C. where they talked about the technical support being made
available to Habitat’s CBA affiliates (and other affiliates). Response
was very positive. Mr. Edward Pollock and George James attended a CBA
luncheon and addressed the group with an introduction into Building America
and our systems engineering approach.
CBA Communications:
A database populated with 226 stakeholders
including Habitat affiliates and congressional staff members. Researchers
use the CBA database for tracking communications, technical assistance,
and progress. In 2006, BAIHP began expanding this database to include
all HFH technical assistance activities.
All of the CBA affiliates received two information packages, one in
the Spring of 2006 and one in the Winter of 2006. Packages included information
on shared goals of CBA and U.S. DOE BA program, resources available to
CBA affiliates, a “Partnership Updates,” and an offer of
BA technical assistance. Three affiliates responded with interest to
the first package with requests for assistance. Package 2 was an update
of CBA-BA activities based on field visits with CBA affiliates in Michigan
in June.
Congressional members and their staff members specializing in housing
and energy issues also received both packages as well. A separate package
was sent to all five Building America teams. BAIHP staff visited the
office of Senator Bill Nelson, a native of Brevard County, home of the
Florida Solar Energy Center, and met with Ms. M. Bridget Walsh, Deputy
Legislative Director, introducing her to Building America program and
encouraging Senator Nelson’s office to participate in the Congress
Building America project.
CBA-BA-RESNET Partnership:
BAIHP worked with Steve Baden at
RESNET to recruit volunteer raters for the effort. RESNET issued a “Call
for Volunteers” in their newsletter in April and in May posted
an article about the partnership on their website along with material
that McIlvaine developed to explain the partnership to the RESNET volunteers.
Response has been very strong and several dozen RESNET members volunteered
within the first month. Materials describing the benefits to RESNET volunteers
are online at: /casestud/hfh_partner/index.htm In
2006, RESNET and HFHI decided to expand the partnership beyond CBA to
accommodate those volunteer raters outside the CBA affiliate areas.
CBA Plan Packages:
The Building
Science Consortium developed full plan packages with complete sets of
building plans (per Mr. Garman and Mr. Pollock’s request), including
building science. BAIHP reviewed the plans specifically for volunteer
friendliness. The packages are available free online at www.buildingscience.com (search
for “Affordable House Plans” or “Congress Building
America”). Habitat International is strongly supportive of this
effort, and has regularly recommended that affiliates review the materials.
CBA-BA Partnership Website:
A map of all CBA affiliates is
posted on /casestud/hfh_partner/index.htm along
with a summary of the partnership, a link to request more information,
an activities update and other communication pieces. An update of BA-CBA
activities has been added to that web page and was distributed to all
participants in CBA.
Certificates of Recognition:
CBA affiliates partnering with
Building America received Certificates of Recognition (approved by DOE).
Affiliate staff showed a surprising interest in them and seemed genuinely
pleased to receive them.
CBA Restructuring:
HFHI recently announced that the CBA program
would be restructured. BA staff awaits details of the changes but plan
to continue working with these progressive affiliates to demonstrate
achievable energy efficiency in affordable housing – setting an
example for the whole building community.
CBA Michigan Affiliates:
While in Michigan for the 2005 Jimmy
Carter Work Project, researchers met with five other CBA-HFH affiliates
who (in addition to Harbor Habitat) responded to BAIHP’s initial
mailing with interest in partnership:
-
Kalamazoo Valley HFH in Kalamazoo, MI
-
HFH of Lansing in Lansing, MI
-
HFH of Monroe County in Monroe, MI
-
Blue Water HFH in Port Huron, MI
-
Lakeshore HFH in Holland, MI
A Congress Building America contract report was written summarizing
the findings of these visits with recommendations and best practices.
The report was distributed all the affiliates, HFHI staff, and the Michigan
Habitat Association, a statewide support arm of HFHI, who requested parametric
analysis for use with their energy efficiency grant program.
HFHI Builders Blitz
The Builders Blitz program grew exponentially during the 2005 and 2006
projects. Designed to draw the local building community into Habitat
partnership, the program teams local home builder associations (HBAs)
with local HFH affiliates. The HBA works out a sponsorship scheme with
its members who usually chip materials, sub-contractors, site supervision,
and volunteers. The affiliate generates local press coverage and introduces
the whole group to the Habitat building process. BAIHP supported two
affiliates participating in the Builder Blitz in the summer of 2005
and 2006 through sub-contractors Calcs Plus in Venice (FL) and Guaranteed
Watt Saver in Oklahoma City (OK). Calcs Plus produced HERS ‘99
ratings, Manual J and D calculations for two Energy Star houses in
the summer of 2005 and three houses in the spring of 2006. GWS produced
the same for 10 homes built by the affiliate in Oklahoma City in the
summer of 2006. In the future, BAIHP will invite more Builder Blitz
affiliates to participate in BA activities.
Gulf Coast Recovery Effort, Recommendations for Rebuilding (September
2005- June 2006)
In the weeks following Hurricane Katrina, HFHI staff called on BAIHP
for assistance with a variety of concerns including guidelines for safely
reoccupying homes, minimizing moisture damage, and priorities for deconstruction
and reconstruction.
Initially, BAIHP provided Energy Star ratings and two Building America
packages for HFHI’s first design for rebuilding. BAIHP’s
major contribution to the recovery effort was support to HFHI’s
Department of Construction and Environmental resources and HFHI’s
Operation Home Delivery (OHD), a new department set up to handle Gulf
Coast rebuilding activities.
Researchers participated in vigorous discourse about how Habitat should
rebuild, responding to in excess of 1000 emails from HFHI staff, HFH
affiliate staff, and other building scientists involved with the recovery
effort including DOE’s Katrina Informal Green Working Group.
BAIHP completed and delivered energy analysis comparing typical Louisiana
construction specs to the new HFHI minimum standards. Annual energy use,
HERS ‘99 ratings (1999 and 2006), IECC compliance were calculated
for each of HFHI’s 8 new floor plans that will be used for both
HFH affiliate site building and modular construction in the Gulf Coast
region. Additional analysis of several improvements was requested and
delivered.
In June, a first draft of construction standards that encompass site
safety, occupant health, building durability, and energy efficiency was
produced with launch scheduled for October of 2006. As the main energy
elements of the standards were finalized, BAIHP provided analysis of
eight designs including Energy Star ’99 rating, HERS ’06
Index, IECC ’03-06 compliance, and projected annual energy use
in comparison to typical specifications (developed with LSU faculty member
Dr. Claudette Reichel.)
In addition to this primary activity, BAIHP staff directed many inquiries
to existing resources, some developed under partial DOE funding. Researchers
also responded to inquires directly from Habitat affiliates in the recovery
region and participated in a number of collaborative activities related
to rebuilding:
- In November of 2005, J. McIlvaine participated in a USGBC technical
design charrette at the GreenBuild Conference in Atlanta to evaluate
the applicability of the new LEED for Homes program to the Habitat
homes to be built in the Katrina Recovery zone. The results indicate
that achieving the “Certified” level of the program is
within HFH capability. These results will be drawn into HFHI planning
activities in the “Operation Home Delivery” department.
J. McIlvaine led the break out session during the charrette related
to energy efficiency and indoor air quality. Two Gulf Coast HFH affiliates
and numerous HFHI staff attended.
- In November of 2005, J. McIlvaine visited HFHI headquarters in
Americus, GA to plan recovery strategies. It was decided that BAIHP
would support construction by the 17 affected HFH affiliates in the
Gulf Coast region and construction by HFHI’s new Operation
Home Delivery Department. The analysis mentioned above served both
audiences.
- In March of 2006, BAIHP researchers conducted a field visit to
the region beginning in Mobile (AL) and traveling west to Gulf Port
and Waveland (MS) then on to Covington and Slidell (LA.) J. McIlvaine
met with HFHI field manager Greg Graves, three HFH affiliates, and
staff at a volunteer-housing camp. The draft standards were discussed
at length and observations were made about the current practice at
the Covington and Slidell affiliates. They reorganized and prioritized
the standards and subsequently drafted a narrative to explain why
the standards were selected. The finished narrative, written by J.
McIlvaine, grouped the standards into three categories: Occupant
Health and Safety, Building Durability, and Energy Efficiency and
Comfort. BAIHP recommended that the narrative be used when introducing
affiliates to the new standards to give affiliates the reasoning
behind the standards. Parts of the narrative were incorporated into
HFHI’s version of the Minimum
Standard but no final document has been issued.
Gulf Coast Recovery, OHD Modular Housing Factory Study
In the seventh budget period, UCF researchers assisted Habitat for
Humanity in the design of a Habitat modular housing factory. The
team assisted with:
-
Selection of an existing facility
-
Identifying the retrofits that will be necessary
-
Layout alternatives for the factory incorporating lean production
principles
The team also recommended changes to interior layouts to open up the
designs, making them more compatible with conventional home designs,
and introduced the issue of factory installation of HVAC equipment and
its effect on production. The UCF-IE research team and FSEC researcher
D. Beal hosted a workshop in May 2006 for Habitat representatives to
review progress in planning the new factory. Revised drafts of the following
design products were presented: value stream map, factory layout and
detailed process descriptions. Lean production principles were embedded
throughout the factory design. Many possible enhancements were discussed
during the workshop. The team followed up by exploring each idea, refining
the factory design to incorporate viable enhancements, and resubmitting
to Habitat.
Ultimately, OHD decided against launching a factory in favor of working
with modular manufacturers. In subsequent months, BAIHP provided contacts
to HFHI in the manufactured housing industry including long time BAIHP
partner Palm Harbor Homes. In a related project, one of OHD’s high
profile sponsors, Oprah Winfrey, worked out the details of a community
with Baton Rouge HFH to be comprised of 15 Palm Harbor modular homes.
In the fall, BAIHP will continue to support this effort providing both
analysis and on-site support during production. All the houses will be
Energy Star qualified.
Habitat Builder Option Packages – HabiBOPs
During the 6th budget period FSEC researchers met with Habitat for Humanity
International staff at HFHI headquarters in Americus, Georgia to discuss
the need and possible solutions for the challenges that Habitat affiliates
face in their effort to achieve Energy Star status.
HFHI drafted a new Habitat initiative named “Habitat Better Built” to
encourage affiliates to embrace energy efficiency, durability, and healthy
indoor air quality as part of a larger move toward increasing construction
capacity. This built from BAIHP efforts in previous budget years to develop
an Energy Star equivalency program (called HabiBOPs) for Habitat affiliates.
The BAIHP-HFHI draft (2002) included a request for EPA analysis of additional
Builder Option Packages (BOPs) for various Climate Zones as a pilot study
for adding BOPs that emphasize envelope improvements over expensive equipment
improvements. The simulation work was never funded and was outside the
scope of BAIHP’s work plan.
With the advent of the 2006 Energy Star New Homes Program, there is
some interest at EPA in evaluating the feasibility of achieving Energy
Star for affordable housing. EPA contacted BAIHP researchers three times
during the final year of the project to discuss concerns that drove the
original HabiBOP effort including the emphasis of equipment efficiency,
rather than envelope improvements, to achieve Energy Star via the National
Building Option Package path as well as the unavailability of raters
in many locations (a concern for all builders – not just Habitat).
HFH affiliates in Jacksonville (FL), Indian River County
(FL), Birmingham (AL) and Houston, TX had all agreed to field test the
pilot HabiBOP program in Year 5 of the BAIHP project.
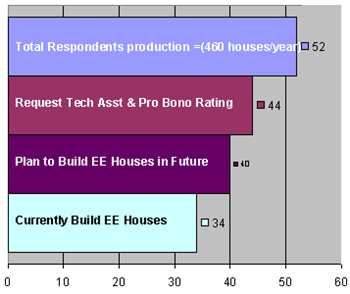 |
Figure 25. Responses to a 2002
BAIHP-HFHI survey of affiliate interest in energy efficiency
and Home Energy Ratings. |
Joint
Grant Proposal
In 2002, BAIHP supported a HFHI proposal to fund writing and production
of a national HFH homeowner’s manual. Homeowner education, particularly
about energy efficiency, indoor air quality, and maintenance issues is
a frequently cited area of weakness in Habitat’s homeownership
program. The proposal was not funded, but HFHI later used a portion of
it to successfully apply for an EPA grant to produce a homeowner guide
about indoor air quality. The electronic version is available free to
all affiliates.
Survey of Affiliate Energy Practices
In 2001 and 2002, BAIHP worked with HFHI to conduct a survey among the
most productive domestic affiliates about current energy practices.
The survey helped to illuminate the progress that HFHI training had
foster since the inception of the Environmental Initiative in 1995
when very few affiliates actively embraced energy efficiency.
Fifty-two affiliates responded (Figure 25) representing a construction
capacity of 460 homes annually. Of the 52 affiliates, 34 indicated that,
after learning about Energy Star in the BAIHP session, they thought that
some of the homes they had built would qualify for Energy Star status
and 44 affiliates indicated that they would be interested in a HERS ‘99
rating if it were available for free and BAIHP design assistance (DA).
Follow up to the survey involved helping affiliates make contact with
a home energy rater in the region to produce a preliminary Energy Star
rating – a precursor to the RESNET-BA-HFHI partnership launched
in the final year of the project
Technology Evaluation
Over the past decade, affiliate interest in alternative building systems
has escalated and BAIHP has frequently conducted simulation analyses
to provide affiliates with performance comparisons.
At the request of HFHI, BAIHP tested a home built by Home Front, Inc.
in Sarasota, Florida. The house scored an 87.6 on the HERS ‘99
scale. Built with structural insulated panels (SIP), which contain a
polystyrene core faced on both sides with a thin concrete board. The
exterior finish is stucco with Hardy board trim. A structural steel wind-frame
welded to steel plates imbedded in the slab was engineered to withstand
hurricane force winds. The panels passed Dade County large missile impact
and wind load testing.
Interior ducts are housed in a central corridor and connect to a heat
pump in a central closet. Return air is drawn from each room through
extra registers on the duct chase. A whole house fan at one end of the
chase provides ventilation during shoulder seasons. Findings were reported
to HFHI.
HFHI 2005 Jimmy Carter Work Project
A team of 4 BAIHP researchers joined the 2005 JCWP in Benton Harbor MI.
Working with Harbor Habitat for Humanity, 2 team members conducted
training of all house leaders (plus some crew leaders) the before the
JCWP began (Saturday), and were in charge of an Energy Crew during
the week-long build that implemented energy efficiency improvements
(air sealing, insulation, crawlspace sealing, and duct sealing) in
20 homes. 2 more BAIHP researchers joined them on Friday and assisted
with the testing of the 20 homes built during the 2005 JCWP.
All 24 homes built in the JCWP 2005 in Benton Harbor were tested and
rated by a local group, WARM Training, soon after the JCWP. All were
Energy Star homes, each featuring a conditioned crawl space, high efficiency
(direct vent combustion) gas furnace, excellent windows, Energy Star
appliances, outside air ventilation, and very low infiltration. Certificates
in “Recognition of Excellence” were prepared for both affiliates
and delivered to Trevor Riggen (HFHI Washington Office). All Benton Harbor
JCWP houses were registered at Energy Star homes and each homeowner received
notice of such with a cover letter from BAIHP.
HFHI 2003 Jimmy Carter Work Project (2003 JCWP)
Habitat International Director of Construction and Environment
requested FSEC assistance for all three Carter Project affiliates: Calhoun
County (AL) and LaGrange (GA). The JCWP affiliate in Valdosta (GA) did
not request BAIHP assistance; however, a former Energy Monitor working
at the Valdosta site organized an informal corps of volunteers to tackle
air sealing and insulation details. The construction manager and executive
director made the 2003 JCWP an example of high performance, high quality
housing for affiliates and other builders in the region and consequently
asked BAIHP for assistance in reviewing construction techniques.
 |
Figure 26. Homeowner Sandy
Sedano installs rigid insulation (part of the energy package) on
her new home during the 2003 JCWP at the Anniston (AL) site.
|
Calhoun County HFH:
The Calhoun County HFH affiliate (Anniston,
Alabama) built 35 near Energy Star homes during the 2003 JCWP.
BAIHP worked closely with the mechanical contractor and the construction
supervisors prior to the build to bring the initial HERS ‘99 ratings
of 78 up to 86. Though the houses had been slated to be Energy Star,
a miscommunication resulted in the air conditioning efficiency being
SEER 10 instead of SEER 12. In Anniston’s mixed-humid climate the
difference was enough to drop HERS ‘99 ratings below the 86 target.
However, the homes are much more efficient than the previous convention
and many volunteers were exposed to energy efficient design and construction
as well as combustion safety design (Figure 26). Radon mitigation
systems were provided by an Alabama environmental group.
Troup-Chambers
HFH (LaGrange, Georgia):
The executive director for this affiliate
adopted the Energy Star goal and spearheaded the construction of 22
Energy Star homes during the 2003 JCWP (Figure 27). Four plans
were rated and scores ranged from 86.5 to 88.5. BAIHP consulted with
the affiliate on window specifications, insulation levels, AC efficiency,
and air sealing details particularly with regard to the air handler
closets which were previously built with return plenums open to the
attic. The affiliate plans to continue building using the JCWP specifications.
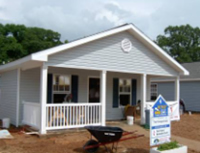 |
Figure 27. 2003
Jimmy Carter Work Project house in LaGrange GA – one
of 22 Energy Star homes built in one week. |
In the final year of the project, BAIHP researchers converted the LaGrangre
HFH write up in the BA Best Practices document into an independent four-page
case study. BAIHP worked with staff at NREL to revise the BAIHP Habitat
Partnership fact sheet to encompass all BA work with Habitat and to produce
2 new Habitat case studies, the LaGrange and another for the HFH affiliate
in Lakeland, FL.
Technical Assistance to Habitat for Humanity Affiliate
During the fifth and sixth budget periods BAIHP’s technical
assistance to Habitat affiliates shifted away from general assistance
to individual affiliates toward focused technical assistance to progressive
affiliates, high production affiliates, and regional and national initiatives
including
- Regional Initiative: Gulf coast rebuilding efforts (described
above)
- National Initiative: Congress Building America and the Builders
Blitz (described above)
- Regional: Ohio’s First Energy grant program for Energy Star
affiliates
- Progressive affiliates in Lakeland (FL), Houston, and Loudon County
(TN), the latter being an ORNL zero energy home initiative with FSEC
monitoring assistance.
A cumulative list of affiliates receiving direct design assistance from
BAIHP is shown in Table 19 at the end of this section. Work
conducted with individual Habitat affiliates, independent of national
and regional initiatives, is presented here, organized by state.
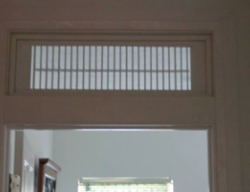 |
Figure 28. Transom
return air pathway with operable louvers blends in with the vernacular
aesthetics of this DESIGN habitat Energy Star home built in conjunction
with Auburn University’s College of Architecture. |
Alabama:
Auburn University
David Hinson from the Auburn University College
of Architecture contacted BAIHP about a prototype “DESIGNhabitat” home.
Three Energy Star homes have now been built with the local Habitat
affiliates in Auburn. The prototype will be offered to affiliates statewide
through the
Alabama Association of Habitat Affiliates (AAHA) and non-profit
Design
Alabama. AHA requested indoor air quality and combustion safety
testing plus design input on the prototype home in 2002 and 2003. The
design features vernacular touches that enhance energy efficiency such
as the screened front porch, operable transoms over doors (for ventilation
and return air flow), metal roofing, and large overhangs
(Figure
28). A sealed combustion closet for the gas water heater, sealed
and tested ducts, and high efficiency heating and cooling complete
the energy package. In February of 2006, BAIHP participated in studio
jury at the Auburn School of Architecture. Competing designs incorporated
modular housing into Habitat’s volunteer construction process.
A winning design was selected for construction. Palm Harbor Homes built
two modules and students construction a joining module on site. The
home will be tested and rated in the Fall of 2006 with participation
from students.
Alabama: Birmingham HFH
In 2001, BAIHP researchers tested and rated 3 homes for this affiliate
and provided the local construction manager with energy analysis and
recommendations. Birmingham HFH continued to build Energy Star homes
in 2004 - many with HUD approved safe room construction.
Alabama: Calhoun County HFH
Please see 2003 JCWP above, in the summary of work conducted with
HFHI.
Florida: Alachua HFH
Florida H.E.R.O. has worked with Alachua Habitat for Humanity for many
years. Currently the affiliate is building a subdivision called Celebration
Oaks. Summary of specifications is provided in Table 17.
Table 17. Alachua Habitat for Humanity Specifications
for Celebration Oaks
Component |
Specification |
Conditioned Area |
~1100 (2 built, 6 in progress, 64
units total) |
HERS ‘99 Rating |
NA |
Cooling and Heating |
SEER 12 Air Conditioning with homeowner
choice of heat pump or standard gas furnace heating, Air handler
in the conditioned space. |
Ventilation |
Filtered passive fresh air ventilation. |
Duct System |
Duct system engineered using Manual
D calculations, sealed with mastic, performance tested for air
tightness |
System Capacity |
Cooling and heating systems sized
using Manual J calculation procedure |
Water Heating |
Standard Gas (considering tankless
gas) |
Walls |
ICF Construction with wood frame
roof and interior walls |
Ceiling |
R-30 cellulose insulation |
Windows |
Double pane Low-E vinyl frame |
Florida: East Orange County HFH
After attending courses and seminars taught by BAIHP staff over several
years, this affiliate’s construction manager began building interior
duct systems. One of those homes was tested in April of 2003 and found
to have good separation from the unconditioned attic above.
Florida: Indian River County HFH
Analysis and recommendations were done for Indian River County HFH (Vero
Beach, FL). In early 2005 (6th Budget Period), this affiliate agreed
to pilot a duct leakage sealing checklist to determine if a prescriptive
protocol can be used to consistently achieve tight ducts as part of the
HabiBOPs pilot project which did not come to fruition. During the final
year of the project, WCI Communities sponsored a house with this affiliate
providing extra grant money to fund green features. Trifecta Consulting
Group, LLC is providing Green Home Certification and BAIHP will provide
the Energy Star rating.
Florida: Jacksonville (HabiJAX) HFH
This affiliate, located in Jacksonville, Florida, is one of Habitat’s
most productive alliances. In anticipation of HabiJAX involvement in
the HabiBOP pilot program, BAIHP completed preliminary HERS ‘99
ratings on planned homes. Follow-up test results indicate that HabiJAX
is a good candidate for the program, particularly after the construction
manager agreed to incorporate a ventilation strategy and energy efficient
lighting into their home designs. This progressive affiliate worked with
FSEC (under another contract) to incorporate solar water heating. This
affiliate is a regional and national pace setter.
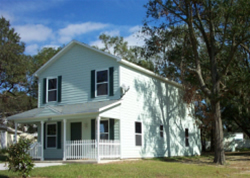 |
Figure 29. Habitat for Humanity
energy efficient home in Lakeland, Florida. |
Florida: Lakeland HFH
Category A: 10 houses
Category B: 1 house
BAIHP has rated 11 Building America level houses that this affiliate
has built since 2002. (Figure 29) The average HERS ‘99
rating was 89.7. Lakeland Habitat Homes Feature:
- Radiant barrier
- Double pane, vinyl frame, low-E windows placed under 24-inch overhangs
to limit direct solar gain
- Houses oriented to limit thermal gain where possible
- Ducts in conditioned space using a framed-in duct chase and interior
air handler closet
- Duct system joints and plenums sealed with water-based mastic and
fiberglass mesh then tested to ensure duct leakage below 5%
- Heat recovery from hot water
- Water-heater timers
- Passive outside air ventilation ducted to the return side of the
air handler with a filter-backed intake grill mounted in the soffit
(at back door or porch)
- 14 SEER air conditioner (up from 10 SEER in 1999)
- Extensive air sealing of building envelope after dry in.
In the
final year of the project, BAIHP researchers wrote a case study with
PNNL about Lakeland HFH.
Florida: Venice HFH
In 2005 and 2006, Venice HFH worked with BAIHP sub-contractor Calcs-Plus.
The affiliate wrote a press release using the BAIHP template and was
written up in the local newspaper (see Builders Blitz description above).
Florida: Space Coast and South Brevard HFH
Since the late 1990’s, FSEC has provided Florida Energy Code calculations
for one of the Habitat affiliates in Brevard County (where FSEC is located.)
Energy Star ratings have been produced for the affiliate (Space Coast
Habitat) over the years with recommendations as requested. In 2004, FSEC
conducted a rating for the other Brevard County affiliate, South Brevard
Habitat. Neither affiliate has yet achieved Energy Star. In the summer
of 2005, the affiliates merged and have not requested any additional
technical assistance.
Florida, Sumter County HFH
This affiliate attended several courses and seminars taught by BAIHP
staff in recent years. As a result, in 2000 the Sumter construction
manager began building interior duct systems. One of those systems
was tested in March 2002, as part of the Air Handler Air Tightness
Study, and found to be connected to the unconditioned attic above.
These results were similar to findings in BAIHP’s sister project
on Interior Duct Systems. After discussions at the April construction
roundtable, modifications were made to the construction approach which
became part of their standard building practice for the affiliate.
Georgia: Atlanta HFH
Energy simulations were conducted for insulated concrete form (ICF) homes
in Houston and Atlanta. Comparative studies could be conducted in both
cities since the same floor plans will be used to build ICF and wood
frame homes in those areas. Simulation results from the homes were evaluated
to develop suggested improvements that would bring the homes to Energy
Star levels. The Houston affiliate is planning a 100-home development
and is looking for home performance strategies that would allow them
to reach Energy Star at a minimum. Simulations using the measured test
data were conducted and recommendations made for their consideration.
The Atlanta home will incorporate substantial thermal mass with concrete
ceilings and concrete interior walls. Simulations on the thermal mass
benefits were completed and reported. These simulations focused on the
use of thermal mass to reduce the size of the heating, ventilation, and
air conditioning systems.
Georgia: LaGrange (Troup-Chambers) HFH
Please see 2003 JCWP above.
Georgia: Sumter County HFH
(See also Plains SIP study in Research with Habitat following Habitat
Technical Assistance)
BAIHP staff worked with the Sumter County HFH affiliate on the Easter
Morning Community from inception in 1995 to completion in 2003. 171 Energy
Star or near Energy Star homes were built between 1997 and 2003. Easter
Morning blitz builds were used as training activities for Habitat’s
Green Team (now defunct). Other energy organizations particularly Oak
Ridge National Laboratory and SouthFace Energy Institute provided excellent
technical assistance to this affiliate, the original Habitat affiliate
based in Americus, GA. As of 2003, Sumter County HFH is no longer building
houses because they have partnered with all qualifying residents to meet
the goal of HFHI’s 21st Century Challenge which is to eliminate
poverty housing in America – one county at a time.
Ohio Affiliates
A utility grant program in Ohio spurred a broad interest among HFH
affiliates in reaching Energy Star level. Affiliate with homes built to
the Energy Star standard in the utility’s service area will receive
a grant that equals the cost of the home. Several affiliates acquired the
Example Energy Star Packages from HFHI’s web site and called to discuss
them. In response to this interest, HFHI conducted a workshop in early
July 2002 attended by sixty people. Subsequently, all affiliates (~30)
attending the course have built and had certified at least one Energy Star
home. Each has collaborated with a local certified HERS ‘99 rater.
Several affiliates contacted BAIHP to clarify aspects of the process and
only one affiliate experienced difficulty with the certifying process and
received direct support from BAIHP.
Louisiana Affiliates
(See Gulf Coast Recovery above)
FSEC arranged a partnership with Superior Environments in Metarie to
provide support to the Baton Rouge HFH affiliate’s April Energy
Star home “blitz build.” Four high efficiency homes were
built during the 2002 blitz build. Though all home met Energy Star
status, documentation has not yet been received that the homes were
registered. (Please see Table 18)
Table 18. HERS ‘99 Scores for
Baton Rouge Habitat Energy Star Homes
House ID # |
Score |
Est. Utilities |
118 |
88. 7 |
959 |
119 |
87.2 |
1122 |
120 |
87.2 |
1364 |
121 |
87.2 |
1120 |
Nevada Affiliates
FSEC was contacted by Portland Cement Association (PCA) to collaborate
on an HFH house planned for the 2003 Builders’ Show in Las Vegas.
This collaboration was a joint effort between BAIHP, PCA, and the Las
Vegas Habitat for Humanity. For more information on the project, visit: http://www.cement.org/countonconcrete/
New Mexico: Albuquerque HFH
BAIHP completed an initial home design analysis for the Albuquerque
HFH which was revised with feedback from the affiliate. Final recommendations
were submitted to Albuquerque HFH to assist them in reaching Energy Star
status.
Texas: Ellis County HFH
This affiliate reports
that they have been building Energy Star homes and now are interested
in moving toward a Zero Energy Home similar to the Loudon County HFH
project in Tennessee.
Texas: Houston HFH
In 2001, BAIHP completed a preliminary evaluation of the concrete homes
built in partnership between Houston HFH and the Portland Cement Association.
Staff tested and rated the homes in January 2002 and made recommendations
for reaching beyond Energy Star to the Building America standard. Later
that year, the affiliate’s construction manager reported that
they were now implementing BAIHP energy efficiency, durability, and
indoor air quality recommendations. Final home design recommendations
included construction of a passive ventilation system and an interior
duct system. In 2004, this affiliate reported that all homes (~100)
built since FSEC’s 2002 recommendations have exceed Energy Star
(rated by local utility) and have passive fresh air ventilation ducted
to the air handler with a separate, soffit-mounted filter. In 2005,
Houston Habitat built dozens of homes for affiliates the Gulf Coast
recovery region.
Washington DC HFH
BAIHP met with DC Habitat’s Executive Director and separately with
the Energy and Environment Committee in November of 2005. Current DC
HFH specifications would be considered “Energy Improved” and
the affiliate was interested in pursuing water conservation and energy
improvements that would be very low first cost. Researchers provided
information and visited a Solar Decathlon home slated to be sited on
DC Habitat land. The house unfortunately was subsequently sold by the
team’s university to cover the budget short fall of the project.
Washington State: Grant County HFH
In 2004, WSU staff began providing technical support to Habitat for Humanity
for two site built projects in Olympia, WA (marine climate) and Grant
Co. (cold climate). Technical support included HVAC design, EnergyGauge
analysis and field testing assistance. WSU continues to evaluate these
homes; final case studies were being completed in the spring of 2006
for inclusion in the Building America Best Practice series.
The Grant country home utilized standard construction materials and
framing, ENERGY STAR HVAC, lighting and appliances. This home moved 100%
of the duct system into the conditioned space; from the attic, crawlspace
and garage where it was to be installed, at little or no additional cost.
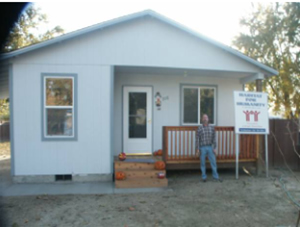 |
Figure 30. HFH of Greater Moses
Lake (WA) Energy Star Home. |
Washington State: HFH of Greater Moses Lake
WSU
BAIHP staff worked with this affiliate to build a home (Figure
30) that was among the first to be certified under the Energy
Star Homes Northwest program in the state. With additional assistance
from Grant County PUD, Habitat exceeded Energy Star program specifications
for heat pump efficiency, glazing, ceiling insulation, lighting and
envelop tightness. Features included:
- Heat Pump HSPF= 8.25 SEER= 13.6
- Air
handler and all duct work in conditioned space
- 4.0 ACH50 tested envelope tightness
- 128 ft2 glazing U=0.32
- Lighting – 95% Energy Star lamps
- Electric water heating EF= .93
- Ceiling R-49
- Floor over crawlspace R-30
- Walls 2x6 R=21
- Energy Star dishwasher
- Whole house ventilation meeting Washington State Ventilation and
Indoor Air Quality Code
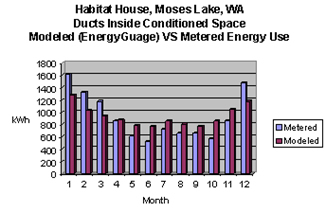 |
Figure 31. Total Metered Use (11,041
kWh)
VS Total Modeled Use (11,107 kWh) |
Built in 2004 in a 6835 heating degree day
climate with four occupants, this all electric home used only 11,041
kWh of electricity (1.1 kWh/ft2-yr) in the first year of occupancy.
Total metered energy use (11,041 kWh) conformed closely to the total
modeled energy use (11,107 kWh) predicted by the Energy Gauge program
(see Figure 31).
Washington State: Greater Puget Sound HFH
In 2004, WSU staff began providing technical support to Habitat for Humanity
for a site built project in Olympia, WA (marine climate). Technical
support included HVAC design, EnergyGauge analysis and field testing
assistance. The Olympia home highlighted the challenges of integrating “green” technologies
such as Icynene insulation and Rastra block walls. The home also used
instant flow gas combo hydronic HVAC and HRV systems, and energy star
lighting, appliances and was built “solar ready”. WSU continues
to evaluate these homes; case studies were completed in the spring
of 2006.
Table 19. Summary of BAIHP
Technical Assistance to Habitat for Humanity 1999-2006
Year |
Project/Location |
State |
Houses/Description |
05-06 |
Gulf Coast Rebuilding Technical
Assistance BAIHP provided on call building science and
energy efficiency technical assistance to any Habitat affiliate
in the Katrina/Rita hurricane impact region. Staff was instrumental
in drafting minimum construction standards for region at the
request of Habitat International. Staff visited the region in
March of 2006 to meet with key affiliates located in Gulf Port
(MS), Covington and Slidell (LA). |
MS
LA |
|
05-06 |
Congress Building America affiliates
Researchers visited with one CBA affiliate in West Virginia and six
CBA affiliates in Michigan (including the Benton Harbor JCWP
affiliate).
All CBA affiliates (nationwide) as well as their congressional
partners received 2 editions of BAIHP’s Partnership
Update and an invitation to partner with BAIHP. |
WV
MI |
Researchers tested 11 houses in West
Virginia and provided the affiliate with recommendations.
1 House
at each of the six affiliates was tested. All affiliates received
a report (Contract Report FSEC-CR-1647-06) with findings, recommendations,
and best practices |
05-06 |
Builders Blitz
Sub-Contractor Calcs Plus provided technical assistance to affiliate
building in Venice Florida during Nationwide Builders Blitz in
both 05 and 06.
BAIHP-RESNET partner Guaranteed Watt Saver provided technical assistance
to the Greater Oklahoma City affiliate. |
FL
OK |
5 houses total – all achieved ’99
Energy Star
10 houses – all ’99 Energy Star |
2005 |
Alachua HFH |
FL |
2 houses completed with a total build
out of 64 |
2005
(June) |
Jimmy Carter Work Project
Training, Energy Efficiency Improvements, Testing Harbor HFH- Benton Harbor, |
MI |
24 Energy Star |
02-05 |
2 Zero Energy Houses
Loudon County HFH & Oak Ridge National Lab
BA fully instrumented two high performance homes to evaluate features
including HPWH, PV, and waste water heat recovery. Data available
on line and streamed to ORNL for analysis; See publication 2004 Christian
et al.
Loudon County HFH, Lenoir City |
|
SIP houses with many features developed
by Jeff Christian at ORNL
2 ZEH (A) |
02-03
(June) |
Jimmy Carter Work Project
Energy Details, Program Development, and Volunteer Training Calhoun County HFH, Anniston Troup-Chambers County HFH, LaGrange |
|
35 Near Energy Star (c)
22 Energy Star (B) |
2003
(Fall) |
Jacksonville Habitat for Humanity
Largest U.S. affiliate; plans to build Energy Star in 2003 and BA
in 2004. Pilot for HabiBOPs Program. HabiJAX, Jacksonville |
|
3 Ratings – near Energy Star (C) |
02-03 |
DESIGNHabitat House – Energy
Efficient Prototype developed by Auburn University and the Alabama
Association of Habitat Affiliates. |
AL |
3 BA – Provided design review,
analysis, rating, and technical support. (B) |
2005 |
DESIGNHabitat House – Energy
Efficient Prototype developed by Auburn University and the Alabama
Association of Habitat Affiliates |
AL |
1 house composed of two modular sections
built by Palm Harbor Homes and one site built section |
2004 |
Grant County HFH
HVAC design and EnergyGauge analysis, Field Testing. |
WA |
|
2002 |
Greater Denver Habitat |
CO |
6 Building America (A) |
01-06 |
Lakeland Habitat, Lakeland |
FL |
10 Category A
1 Category B |
2001 |
Birmingham HFH |
AL |
3 homes tested and rated |
1997-2003 |
Easter Morning Build Sumter County Habitat, Americus |
GA |
117 Energy Star (B)
On Site Training and testing |
2000 |
Jimmy Carter Work Project New York City HFH, Harlem Sumter County HFH, Americus |
NY
GA |
Volunteer and Homeowner Training with
HFHI
Produced 23 Ratings (C) |
98-01 |
Broward County HFH |
FL |
40 Energy Star (B) |
99-03 |
Brevard County HFH |
FL |
20 Energy Improved (C) |
99-01 |
Energy Fact Sheets
Developed by organizations supporting HFHI. |
USA |
BA reviewed/contributed to various
documents |
97-99 |
Easter Morning Community Sumter County HFH, Americus |
GA |
125, Most Energy Star (B) |
98-03 |
Greater Houston HFH |
TX |
97-65 Energy Star Houses (B)
98-100 Energy Star Houses
02-began striving for BA (B) |
97-00 |
Greater Canton HFH, Canton |
OH |
20, Energy Improved (C) |
99-01 |
Durham County HFH, Durham |
NC |
20, Energy Star (B) |
1997 |
Jimmy Carter Work Project |
TN, KY |
50 Energy Improved (C) |
95-97 |
Energy Affordable House Greater Houston HFH |
TX |
65 Energy Improved (C) |
|
Design Assistance and Energy
Analysis |
|
|
|
|
|
|
02-06 |
Design Assistance and Energy
Analysis
DC: Washington DC HFH
FL: Pasco, Orange, Brevard Counties, Indian River County
GA: Atlanta HFH
NM: Albuquerque
NV: Las Vegas HFH
OH: Clark, Geauga, Lorain, Marion, & Morrow Counties;
Firelands.
OK: Central Oklahoma
PA: Greene County
TX: Lubbock, Smith County KY: Greater Louisville |
|
|
00-01 |
AL: Birmingham
MS: Jackson |
AL |
1 Energy Star Cert (B) |
98-99 |
CA: Long Beach HFH
DE: Wilmington HFH
FL: Indian River, Lake, & Sumter Counties,
MI: Grand Rapids HFH
NY: Albany, Syracuse, & Yonkers
VA: Lynchburg HFH |
|
|
II. Research with Habitat for Humanity
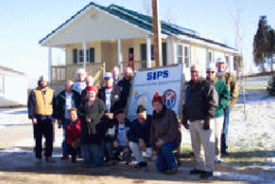 |
Figure 32. Local sponsors in
front of 2nd ZEH built by Loudon County HFH in partnership with
ORNL. FSEC provided monitoring for the 1st and 4th ZEHs |
Tennessee: Loudon County HFH
At the request of ORNL Buildings Program Director Jeff Christian, BAIHP
instrumented a third zero energy home (ZEH) built by Loudon County
(TN) HFH (Figure 32) in the final year of the project. ORNL
has built more than four such homes with the affiliate, and BAIHP previously
instrumented and collected data on ORNL’s behalf from Loudon
County’s first ZEH which showed results of $80 net annual electric
cost and an ACEEE paper was authored by ORNL and FSEC. BAIHP assisted
with data collection on the fourth ZEH also. The affiliate has provided
valuable feedback on the SIP construction process to other interested
affiliates. Data is available on-line at www.baihp.org in
the “Current Data” section of the site.
West Virginia: Almost Heaven HFH
During
the final year of the project, BAIHP commenced instrumentation of a
SIP house with radiant floor heating built by Almost Heaven HFH’s
(Franklin WV), a CBA affiliate. Actual data on the performance of radiant
slab heating systems is scant; however, there are many claims of energy
savings and greatly improved comfort. BAIHP staff members were on hand
for the construction and pouring of the radiant slab. Instrumentation
consists of temperature probes embedded in the ground 1 and 3 meters
from the slab, on the sides of the slab, and at three interior locations
under and in the slab; the middle of the house, 1 meter form the edge
of the slab, and in between these two locations. When the house is
completed, and heating equipment is set in place, a final trip to complete
the instrumentation will be carried out. At the end of this Budget
Period, construction of the house was still under way with completion
anticipated in the fall of 2006 or early in the spring of 2007.
Structural Insulated Panel Construction Study
Plains, GA (Sumter County HFH, now defunct)
Most of Habitat's 1400+ American affiliates build wood frame houses.
However, some affiliates are experimenting with other systems including
straw bale construction, ICFs, and SIPs. Sumter County Habitat for Humanity,
the original affiliate started by Habitat founder Millard Fuller, partnered
with the Department of Energy and the Structural Insulated Panel Association
(SIPA) to build two SIP houses in Plains, Georgia. This field project
seeks validation of heating energy savings
from SIPs.
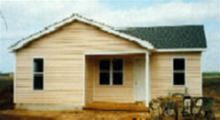 |
Figure 33. Energy Use in this
Sumpter County Habitat Home, Built with Conventional 2x4 Framing
in Plains, GA, was Compared to SIP Construction |
The affiliate built the two SIP houses and a frame house on three neighboring
lots. The Structural Insulated Panel Association (SIPA) provided some
assistance with the SIP houses. The three houses were intentionally built
with their calculated energy performance (HERS ‘99 score) similar
to each other as seen in Table 20. The frame house (Figure
33) featured energy related details typical for the affiliate which
resulted in an ACH50 of 5.3. With the home's whole-house fan cover installed
the ACH dropped to 3.9, very good for frame construction. However, testing
results revealed much better performance in the SIP houses with a measured
ACH50 of 1.8. Though this indicates a 50% decrease in infiltration, that
does not correlate directly into a 50% heating energy savings since infiltration
determines only a portion of the total heating energy use. Other factors
include insulation levels, conditioned square footage, window area, number
of occupants, occupancy patterns, use of supplemental heaters, heater
operation strategy, and indoor temperature. Monitoring equipment was
installed to measure total, heating, and water heating energy use, as
well as indoor and outdoor temperature.
Table 20. Sumter County (GA) Habitat
for Humanity Field Study
House |
Structural System |
ACH50 |
Average Hourly Indoor Temp. (F) |
Condit. Floor Area (sq. ft.) |
HERS ‘99
Score |
1 |
SIP |
1.8 |
75 |
1036 |
82.7 |
2 |
SIP |
1.8 |
75 |
1069 |
83 |
3 |
Frame |
5.3 |
80 |
1208 |
82.9 |
A 1995 study of 10 Habitat homes in Florida City, Florida revealed that
the maintained indoor air temperature heavily influences conditioning
energy use (Parker, et al. 1995). Analysis suggests that this may be
a significant factor in this Sumter County study. The frame house consistently
maintained a higher indoor temperature than the SIP houses. The impact
of this considerable difference (average of 5F) is accounted for an analysis
of heating energy use (per 1,000 ft2 of conditioned space) relative to
the indoor to outdoor temperature difference. This revealed that the
SIP houses saved 25% compared to the frame house.
A previous study conducted in Louisville, Kentucky comparing SIP to
frame construction found a 15% savings for the SIP construction (Rudd,
1997). In that study, the duct systems for both houses were located in
conditioned spaces. The Plains SIP houses had ducts in the conditioned
space while the frame house had ducts in the unconditioned attic. The
10% difference in the Plains and the Louisville findings are attributed
to the differences in duct system locations. Together, these two studies
suggests that homes of 1,200 ft2 and smaller stand to gain significant
energy performance from SIP construction with heating energy savings
of 15-25% depending on duct location and average indoor-outdoor temperature
differences.
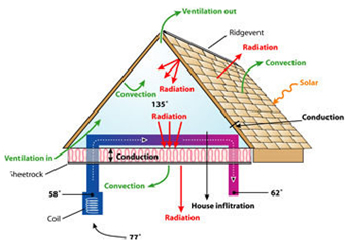 |
Figure 34. Vented Attic Thermal
Processes |
BA Roofing Study with Lee County HFH (FL)
Ft Myers, Florida
Roof and attic thermal performance exert
a powerful influence on cooling energy use in Florida homes. Unshaded
residential roofs are heated by solar radiation causing high afternoon
attic air temperatures. The large influence on cooling is due to increased
ceiling heat transfer as well as heat gains to the duct systems which
are typically located in the attic space (Figure 34).
The
Florida Power and Light Company and the Florida Solar Energy Center instrumented
six side-by-side Habitat homes in Ft. Myers, Florida (Figure35)
with identical floor plans and orientation, R-19 ceiling insulation,
but with different roofing systems designed to reduce attic heat gain.
A seventh house had an unvented attic with insulation on the underside
of the roof deck rather than the ceiling:
- (RGS) Standard dark shingles (control home)
|
- (RWB) White "Barrel" S-tile roof
|
- (RWS) Light colored shingles
|
- (RWF) White flat tile roof
|
- (RSL) Standard dark shingles with sealed attic and R-19 roof
deck insulation
|
- (RTB) Terra cotta S-tile roof
- (RWM) White metal roof
|
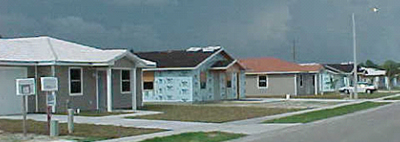
Figure35. Street scene showing
the three closest homes
(from left: white "barrel" s-tile
(RWB), terra cotta s-tile (RTB) and white metal (RWM)).
All seven houses were completed by June 26th, 2000 with extensive testing
to assure the buildings were similar. Each home was monitored simultaneously
from July 8th - 31st in an unoccupied state.
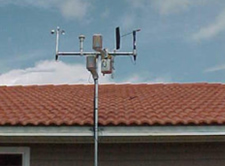 |
Figure 36. Project Meterological
Station |
Building thermal conditions and air conditioning power were obtained
on a 15-minute basis. Each of the examined alternative constructions
exhibited superior performance to dark shingles. Figure 37 plots
the maximum daily air temperature to the maximum recorded at mid-attic
in each construction. Figure 38 shows the average daily attic
air temperature profile.
The maximum attic temperature during the peak summer hour is 40 F greater
than ambient air temperature in the control home while no greater than
ambient with highly reflective roofing systems. Light colored shingles
and terra cotta roofs show temperatures in between. Table 21 summarizes
the metered data from the unoccupied period and Figure 39 shows
the variation in space cooling load profiles in the test homes.
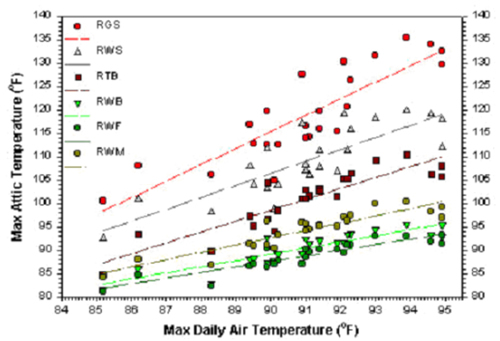
Figure 37. Relationship
of peak air to peak attic temperatures.
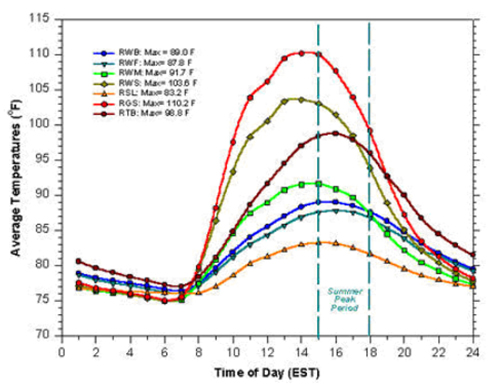
Figure 38. Average attic
air temperatures over unoccupied period.
Table 21. Cooling Performance During
Unoccupied Period July 8th - 31st, 2000
Site |
Total
kWh |
Total
Savings
kWh |
Total Saved
Percent |
Cooling
Demand
kW |
Cooling
Savings
kW |
Cooking
Savings
% |
RGS (base) |
17.03 |
---- |
---- |
1.63 |
---- |
---- |
RWS |
15.29 |
1.74 |
10.2% |
1.44 |
0.19 |
11.80% |
RSL |
14.73 |
2.30 |
13.5% |
1.63 |
0.01 |
0.30% |
RTB |
16.02 |
1.01 |
5.9% |
1.57 |
0.06 |
3.70% |
RWB |
13.32 |
3.71 |
21.8% |
1.07 |
0.56 |
34.20% |
RWF |
13.20 |
3.83 |
22.5% |
1.02 |
0.61 |
37.50% |
RWM |
12.03 |
5.00 |
29.4% |
0.98 |
0.65 |
39.70% |
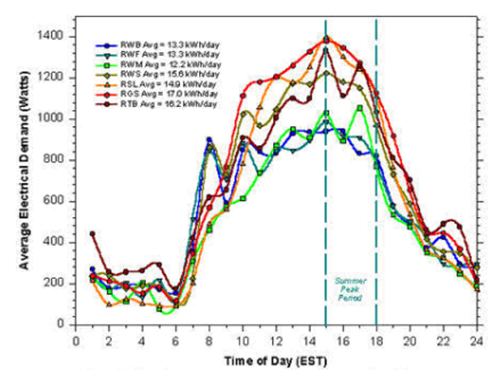
Figure 39. Average space
cooling demand and profiles over the unoccupied period.
The above results are for the 1,144 square foot homes in
the study. Since savings largely scale with ceiling area, the kWh and
kW values should be normalized by the applicable ratio. For instance,
typical FPL homes of 1,770 square feet would have estimated absolute
savings 55% greater than above. Also, normalizations were made for slightly
different thermostat set points and the measured performance of individual
AC units.
Table 22. Summary of Normalized Savings
and
Demand Reductions from Regression Estimates
Case Description |
Cooling Savings |
Peak Demand Reduction |
kWh |
Percent* |
kW |
Percent* |
RGS(Control) |
--- |
--- |
--- |
--- |
RWS (White Shingle) |
300 |
4% |
0.48 |
17% |
RSL (Sealed Attic) |
620 |
9% |
0.13 |
5% |
RTB (Terra Cotta Tile) |
180 |
3% |
0.36 |
13% |
RWB (White S-Tile) |
1,380 |
20% |
0.92 |
32% |
RWF (White Flat Tile) |
1,200 |
17% |
0.98 |
34% |
RWM (White Metal) |
1,610 |
23% |
0.79 |
28% |
* Percentages relative to typical values
for average sized detached South Florida homes detailed in Appendix
H of the original report. |
Additional monitoring took place over a month long period
with the homes occupied, but the thermostat set points were kept constant.
Although average cooling energy use rose by 36%, analysis indicated no
decrease to savings or demand reduction from the highly reflective roofing
systems. The added heat gains from appliances and people increase cooling
system run-time causing the duct system to run for longer periods to
exchange heat from the often hot attic space.
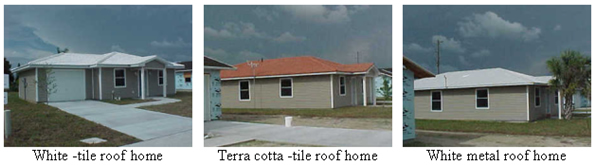
Figure 40 Examples of different
roof materials used.
The results in Tables 21 and 22, show essentially two classes
of performance: white shingles, terra cotta tile and sealed attic construction
which produce energy savings of 200 - 600 kWh/yr and demand reductions
of 0.05 - 0.5 kW. Highly reflective roof systems produce energy savings
of 1,000 - 1,600 kWh with demand reductions of 0.8 - 1.0 kW. A separate
analysis of the data using a special version of the DOE-2.1E computer
simulation verified the magnitude of the measured energy and demand reductions.
In summary, this evaluation strongly confirms the energy-saving benefits
of using more reflective roofing systems in Florida. Selection of colors
with higher solar reflectance will result in tangible cooling energy
savings for customers. This is particularly true for roofing materials
such as tile and metal, which are currently available with solar reflectance
of 65%-75% range. The selection of reflective roofing systems represents
one of the most significant energy-saving options available to homeowners
and builders. Such systems also strongly reduce the cooling demand during
utility coincident peak periods and may be among the most effective methods
for controlling demand.
Training with Habitat for Humanity
BAIHP participates regularly in Habitat regional and national conferences
providing 1 hour, 2 hours, or 4 hour sessions on building science topics
including the BA systems engineering approach. More detail on this
activity is included in the “BAIHP Training” portions
of this report. A summary of training activities is provided here:
-
Southeastern HFH Conference 1996 – 2006
-
HFHI 20th Anniversary 1997
-
Florida HFH Conference 1998
-
Cocoa, FL Building Science Focus Training 1999
-
Syracuse, NY Building Science Focus Training 1999
-
Affordable Comfort 2 day HFH Training 1999
-
Portland, OR Building Science Focus Training 2000
-
New York City, NY JCWP Homeowner Energy Course 2000
-
Florida Construction Roundtable 2001
-
Top 40 Conference 2001
-
Ohio Building Science Focus Training 2002
-
Central Atlantic Regional Conference 2004
-
National Leadership Conference 2004
-
National Urban Conference 2005
-
Florida Construction Roundtable 2005
-
Pacific North West. Construction Roundtable 2005
-
USGBC Charrette for Habitat’s Gulf Coast Recovery,
2005
-
National Leadership Conference/ Urban Conference 2005
-
Western States Leadership Conference/Rural Conference 2006
-
Phoenix, AZ National Building Science Focus Training 2006