Technical
services provided to the HUD Code and modular industry
Contacts:
1.
Introduction
The Building America Industrialized Housing Partnership
(BAIHP) team is one of five Building America teams competitively
funded by the US Department of Energy, Office of Energy
Efficiency and Renewable Energy-Building Technologies program.
BAIHP is led by the Florida Solar Energy Center (FSEC) of
the University of Central Florida (UCF). Team members include
the Washington State University Energy Program and the UCF
Department of Industrial engineering. BAIHP was established
on September 1, 1999 to focus on improving the energy efficiency,
durability, and indoor air quality in HUD Code manufactured
homes.
Figure E-1 shows the US housing sectors by housing type.
While focusing on the HUD code and modular housing sectors,
BAIHP is active in all these housing sectors and has a wide
national network of collaborating builders, suppliers, and
other team members (Please see Figure E-2). The BAIHP team
provides technical assistance to about 30 site builders
and modular home manufacturers including Habitat for Humanity
affiliates throughout the nation.
BAIHP
also is working to enhance the energy efficiency and learning
environment in portable classrooms in the Northwestern states
of Washington, Oregon, and Idaho.
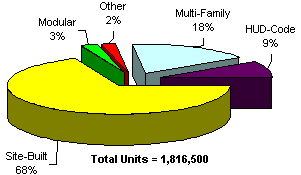 |
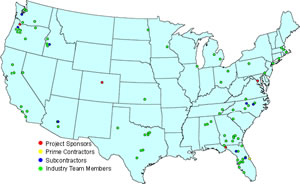 |
Figure
E-1. 2002 housing by type |
Figure
E-2. BAIHP is all over the map! |
2.
Technical Assistance
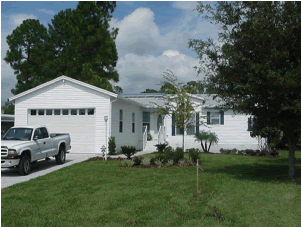 |
Figure
E-3. An
Energy Star home manufactured from Palm Harbor Homes,
Plant City, FL. |
Through
August 2002 (the first three years of the project), BAIHP
has assisted in the construction of more than 5,600 homes
built to Energy Star levels of energy efficiency (HERS score
of >=86). (Please Figure E-3 for example home.) An additional
10,400 manufactured homes have been built 30% to 50% better
than the HUD code as a result of BAIHP efforts - missing
the Energy Star mark by just 0 to 5%. Moreover, an additional
46,000 homes have been produced by team members with air
tight duct systems through end of 2002. To date, BAIHP researchers
have provided technical assistance to more than 31 HUD code
or modular manufacturers at over 60 factories.
Technical
services provided by the BAIHP team includes:
- Third
party certification as part of the Super Good Cents (SGC)
program
-
Energy Star plant certification
- Training
of in-plant personnel and retailers
- Design
approval and home certification as part of SGC program
- In
plant quality assurance quarterly visits
- Tracking
and Documentation (web based)
- Building
science research and testing (duct leakage, envelope leakage,
HVAC and ventilation fan flows, moisture and comfort problem
diagnosis and solution)
- Evaluation
and adoption of new technology and systems (ventilation,
duct, heating and cooling, solar ready, zero energy photovoltaic
systems including development of specifications to assure
quality factory construction )
-
Random field testing and inspection
-
Dissemination of research results to industry, SAA, COSAA,
HUD, NFPA501
Details
of Technical Assistance Provided to HUD Code and Modular
Manufacturers
Technical assistance has been provided to over 31 HUD code
and modular manufacturers (over 60 factories) as listed
below.
HUD CODE MANUFACTURED HOME BUILDERS
- Cavalier Homes (Addison
, AL)
Plant visit, problem home testing.
- Champion
Homes (Redman - Plant City, FL + OR+ID)
Energy Star plant certification in FL, SGC/NC in ID and
OR.
- Champion
Homes (Silvercrest in OR)
SGC/NC.
- Clayton
Homes (TN, GA)
Plant visit.
- Fleetwood
Homes (ID, OR, WA, FL , GA)
SGC/NC in ID, OR, WA; Plant visits, problem home testing
in FL and GA. Coordination with corporate offices in Riverside,
CA.
- Fuqua
Homes (OR)
SGC/NC.
- Golden
West Homes (OR)
SGC/NC.
- Guerdon
Enterprises (ID)
SGC/NC.
- Hi-Tech
Homes (IN)
Plant visit.
- Homebuilders
NorthWest (OR)
SGC/NC.
- Homes
of Merit (FL)
Plant visit.
- Karsten
Company (CA, OR)
SGC/NC.
- Kit
Manufacturing (ID)
SGC/NC.
- Liberty
Homes (OR)
SGC/NC.
- Marlette
Homes (OR)
SGC/NC.
- Nashua
Homes (ID)
SGC/NC.
- Oakwood
Homes (GA, TX)
Plant visits, energy analysis.
-
Palm Harbor Homes (OR, FL, TX, OH, NC, AL, AZ)
Plant Visits, problem home testing, energy analysis, Energy
Star Plant Certification for FL, NC and OH, SGC/NC in
OR, assistance to implement duct blaster testing of airtight
duct construction in all factories, side-by-side testing
in NC documenting 70% savings in heating and 55% in heating,
cooling and domestic hot water. Moisture and indoor air
quality research. Coordination with corporate office in
Texas.
- Skyline
Corporation (OR)
SGC/NC.
- Southern
Energy Homes (AL, TX)
Plant visits, problem home testing, Energy Star plant
certification in AL, duct blaster testing to begin in
spring 2003 in all five AL factories.
- Valley
Manufactured Housing (WA)
SGC/NC.
- Western
Homes (CA)
SGC/NC.
MODULAR
BUILDERS
- All American Homes (NC)
Plant visit. Energy analysis.
- Avis
America Homes (PA)
Plant visit, energy analyses, factory simulation modeling,
shop floor
information systems, integration of lean production principles
in plant
expansion.
- Cardinal
Homes (VA)
Plant visit, energy analyses, factory simulation modeling,
integration
of lean production principles in plant expansion.
- Epoch
Corporation (MA)
Plant visit, factory simulation modeling, lean manufacturing
improvements..
- Excel
Homes (WV)
Plant visit, factory simulation modeling, integration
of lean
production principles in new factory.
- General
Homes (MI)
Plant visit, energy analyses.
- Genesis
Homes (NC)
Plant visit, technical assistance to corporate director
of engineering on Energy Star homes, green home checklist,
2002 Builders Show home.
- Nationwide
Homes (GA)
Plant visit, energy analyses.
- The
Homestore (MA)
Technical assistance to reduce construction cycle time,
energy analyses.
Definitions:
Plant Visit - Written reports are provided. Activities
include one or more of the following
•
discussions with technical and management personnel
• training of line workers
• on-line and off-line testing of homes
SGC/NC
- Super Good Cents / Natural Choice program in the Pacific
Northwest. Activities include quarterly plant visits and
reports, installer training, continuous refinement of technical
standards, co-branding with Energy Star, testing of problem
homes, periodic telephone conference calls. All SGC manufacturers
are Energy Star as well having signed MOUs with EPA and
have built Energy Star homes.
Problem
Home Testing - Researchers test problem homes in the
field and provide written recommendations. Problem homes
exhibit one or more of the following:
•
mold, soft walls, or buckled floors or other moisture related
problem
• high utility bills
• comfort problems
3.
Research Highlights
3.1 Moisture Problems in HUD Code Homes
Alleviating moisture problems is the highest priority research
item of the HUD code industry. Buckled floors, moisture
damaged walls, extensive mold, and other moisture problems
are routinely found in new manufactured homes in the hot,
humid Southeast. Figures E-4 through E-7 show some examples
of the typical problems found.
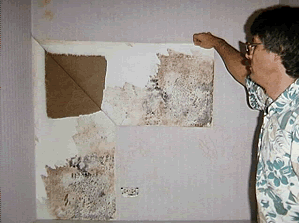 |
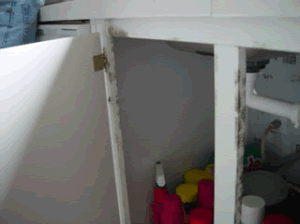 |
Figure
E-4. Mold behind vinyl wallpaper. |
Figure
E-5. Mold under sink. |
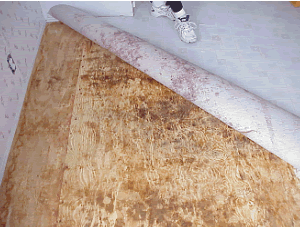 |
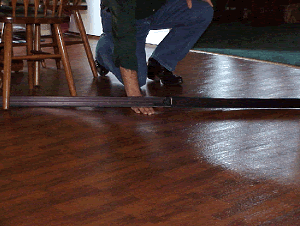 |
Figure E-6. Mold
stain on vinyl flooring. |
Figure E-7. Warped
vinyl floor covering. |
BAIHP
researchers who have field tested more than 35 homes from
five manufacturers, have identified root causes for the
moisture damage and have recommended solutions which were
published in a peer reviewed ASHRAE article. BAIHP also
provides training to field service personnel, collaborates
with the Manufactured Housing Research Alliance and conducts
laboratory studies to develop buckle resistant flooring
materials. Palm Harbor Homes has wholeheartedly adopted
BAIHP suggestions in all of its homes and now tests every
home with a ductblaster in the factory. Not a single moisture
problem has been documented at PHH since BAIHP recommendations
were implemented at the factory. This is a far cry from
the large number of complaints logged prior to implementation.
The cost per home to employ airtight duct systems and return
air transfers is less than $15!!
Requests
for assistance to inspect and diagnose come from the following
groups: Manufacturers, dealers, MH state associations, State
administrative agencies, homeowners, State Energy Offices
a and utilities. BAIHP participation in state installer
training has helped to reduce set-up problems.
FSEC
procured a manufactured housing lab (MHLab) to conduct systematic
research on ventilation and indoor air quality and (IAQ),
and to provide hands-on training. (Please see Figure E-8).
The MHLab features two different HVAC systems each with
its own complete duct system and a variety of supply, exhaust,
and balanced ventilation systems. Occupancy is simulated
with computer controlled lights, showers, and dishwasher
use. More than 60 channels of data can be collected.
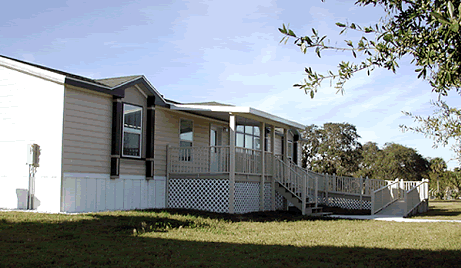 |
Figure
E-8. The
Manufactured Housing Lab (MHLab) at FSEC. |
3.2
Field Monitoring
Several houses and portable classrooms are being monitored
and collected data is displayed on the web at http://www.infomonitors.com/.
Of special interest is the side-by-side monitoring of two
manufactured homes on the campus of the North Carolina A
& T State University (NCA&TSU) in Greensboro North
Carolina (Figure E-9) where the advanced energy efficient
home saved 70% in heating energy over the neighboring control
home (Figure E-10)!
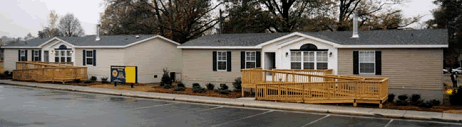 |
Figure
E-9.
Side by side NCA&TSU homes. |
|
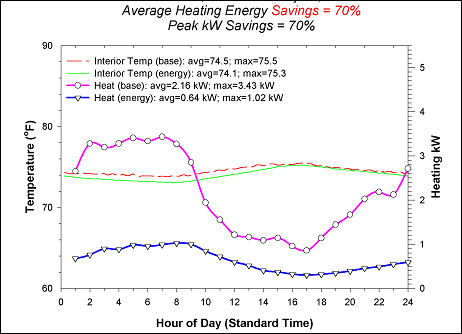 |
Figure
E-10.
Heating season savings. |
The
cooling energy savings was 33% during the summer of 2002.
The water heating savings was also 33% and the combined
Heating, Cooling and Hot water energy savings was 55%.
A
recent effort has begun to test side-by-side a zero energy
manufactured home and an Energy Star home in Idaho. These
homes were built by Kit manufacturing.
3.3
“Cool” Roofs and Unvented Attics
Seven side-by-side Habitat homes were tested under unoccupied
conditions in Ft. Myers to examine the effects of alternative
roofing strategies. After normalizing the data to account
for occupancy, minor differences in house set points, and
equipment efficiencies, the sealed attic configuration was
determined to save 9% and the white roofs about 20% on cooling
energy when compared to the base-case home (tests conducted
during the summer season in South Florida). The base-case
or control roof included dark shingles. A summary of these
comparisons can be found at http://www.fsec.ucf.edu/bldg/pubs/cr1336/CR1336.HTM.
Research on a variety of cool roofs, including the new infrared
reflecting metal roofing, continues at the FSEC Flexible
Roof Facility. (Please see Figure E-11.)
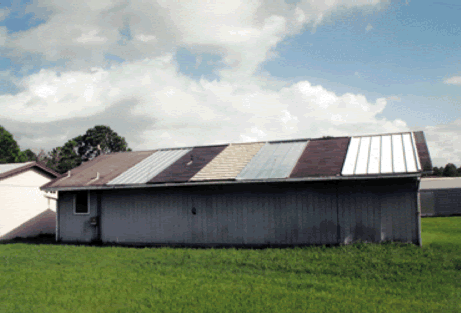 |
Figure
E-11.
Six cells from 2002 roofing experiments.
Cell #1 begins on the left, with Cell #6 located at
the far right. |
3.4
“Green” Housing
A draft point-based standard for constructing green homes
in Florida has been developed and can be viewed at http://www.floridagreenbuildings.org/.
BAIHP
researchers are participating as building science, sustainable
products advisor to the HUD Hope VI project in Miami. This
project’s mission is to redevelop an inner city area
by building 500+ new affordable and energy efficient housing
units.
3.5
Healthy Housing
BAIHP researchers are participating in the creation of national
technical and program standards for the American Lung Association
Health House® program. Two successful media events were
held during 2001 and 2002 educate the public on healthy
housing concepts. Health House builder training was conducted
in March, 2003 and will be offered again as part of the
SouthEast Builders conference in July, 2003.
BAIHP
has conducted and published significant research on whole
house ventilation in HUD code homes, and has improved whole
house ventilation systems in thousands of BAIHP/Energy/SGC
home in the Pacific Northwest.
3.6
EnergyGauge USA®
This FSEC developed software uses the hourly DOE 2.1E engine
with FSEC enhancements and an user-friendly front end to
accurately calculate home energy ratings and energy performance.
The newest version, 2.0, also can analyze photovoltaic and
solar water heating systems. The software is available now.
Please visit http://energygauge.com/
for more information.
3.7
Industrial Engineering Applications
Engineering researchers from the University of Central Florida
Housing Constructability Lab (HCL), a research lab in the
UCF Department of Industrial Engineering and Management
Systems, have provided the following research assistance
to the industrialized housing industry: lean factory design,
energy performance benchmarking, quality management systems,
shop floor information systems, and lean finishing on-site.
Lean
Factory Design
HCL researchers participated in the grand opening of Excel
Homes’ new modular production facility in Ghent, WV.
Excel Homes is one of the largest modular producers in the
U.S., and the new factory will increase Excel’s production
capacity by about 50%. HCL researchers provided technical
assistance in the design of the new operation, incorporating
lean manufacturing principles and making the new factory
more flexible, responsive, and efficient. To test these
concepts, researchers developed a computer simulation model
(please see figure E-12) of the proposed new factory. Innovations
implemented in the new factory included supersize drywall,
replacement of drywall screws with foam adhesive in walls,
industrial manipulators and mechanized material bridges,
pairwise line movement, off-line roofing and ceiling drywall,
and specialized off-line customization bays.
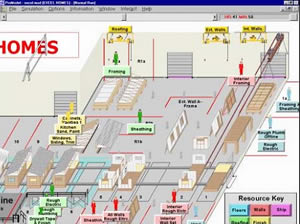 |
Figure
E-12.
Factory Simulation model: Framing |
Benchmarking
Energy Performance
HCL researchers have devoted considerable effort developing
the thesis that energy performance is a key measure of quality
for modular housing. Energy performance affects homebuyers,
impacting their health, safety, home durability, comfort
and energy costs. To increase the visibility of energy performance
within the modular industry, the HCL team developed and
initiated an industry-wide energy benchmarking effort. Baseline
energy performance for selected modular manufacturers was
measured and compared with competitors within and outside
the modular industry. Findings were summarized in a report
for each participating manufacturer, documenting the performance
of each home tested and outlining a cost-effective approach
to upgrade the home to Energy Star levels of performance.
Homes were tested for envelope and duct air-tightness and
inspected to identify specific opportunities for improvement.
Energy analyses indicated that most homes could reach Energy
Star levels (HERS 86) by tightening the envelope and ducts
and by adding a programmable thermostat. Other homes required
more extensive improvement, including additional duct insulation
and more efficient heating/cooling systems.
Quality
Management Systems
The UCF Housing Constructability Lab research team addressed
the following issue for modular housing industry leaders.
“Recommend practical and useable quality control practices
that can be used in modular manufacturing.” To develop
an industry baseline, the team performed a series of quality
system reviews for modular manufacturers who indicated that
they had a formal quality system. During each on-site review,
researchers interviewed company executives as well as functional
management in charge of production, quality, sales, engineering,
purchasing, and customer service. Researchers also accompanied
inspectors as they walked the line. After establishing a
baseline for the modular industry, researchers went in search
of best practices being used by acknowledged quality leaders
in the broader housing industry as well as other industries.
Researchers identified seven fundamental concepts that were
common in the quality leaders and documented numerous best
practices for each concept. Researchers also explored options
for incorporating quality-based metrics into employee incentive
programs.
Factory
Floor Information Systems
HCL researchers continue to identify and develop innovative
information systems for the modular factory floor. The development
of several software prototypes is underway, both involving
production labor. The Status Tracking and Control System
(STACS) is a real time labor data collection and reporting
system. Production workers use wireless laser scanners to
verify their current work assignment, including employee
#, module # and activity #. Scanned information is transmitted
immediately to a base station and then to a local laptop,
where it is verified and temporarily staged. Information
is periodically transmitted via wireless LAN to a central
database computer where it is stored and used for reporting.
A working prototype of STACS was successfully tested in
a large modular manufacturer (please see figure E-13).
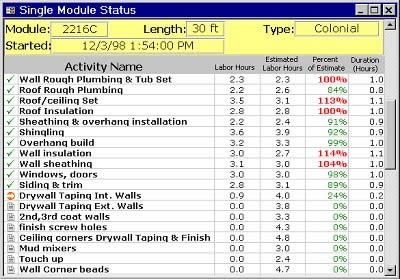 |
Figure
E-13.
STACS Real time production status by module |
The
Expert Labor Forecaster (ELF) is a labor estimating and
planning tool based on the expert opinions of experienced
production staff. These experts identify specific design
features, termed key drivers, that contribute to varying
labor requirements. ELF uses this expert knowledge to estimate
the labor required for each manufacturing activity for a
specific module. When coupled with a production schedule,
ELF can project labor requirements for every activity on
the production floor for any moment n time. ELF projects
the following for each production activity: 1) the specific
module being worked during each production cycle, 2) the
projected cycle time assuming all available staffing is
used, and 3) the minimum staffing required to complete the
activity in the desired cycle time. To assist in labor planning,
ELF highlights activities that are projected to have insufficient
or excess labor. ELF can be used to assist in product costing/pricing,
line sequencing and labor scheduling.
Leaning
the On-site Finish Process
HCL researchers worked with one of New England’s largest
modular builders in an effort to improve their on-site modular
finish process. Using findings from a kaizen rapid improvement
event held in 2001, the builder has been successful in improving
both the operation and the quality of their homes. |