II.
BAIHP Technical Assistance (T-W)
- Timeless
Construction
Long Island, New York
Technical
Assistance by BAIHP Researchers Subrato Chandra and Dave
Chasar
This custom builder planned to build a large energy
efficient custom home in New York with photovoltaic (PV)
grid-connected panels. Discussions began on optimizing
electrical energy use and including solar water heating
panels for household water. The builder planned to use
gas appliances wherever possible and a floor radiant
heating system (pump energy is one-third that for a fan
air distribution system). FSEC recommended a solar water
heating system with gas backup and forwarded information
on two solar water heater designs available from Duke
Solar. FSEC also provided several choices in heat recovery
ventilator (HRV) units which would provide 200 CFM of
outside air.
New
construction drawings were received and EnergyGauge USA
analysis results were discussed with the builder and Alten
Design, since PV grid-interconnect requirements and architectural
changes were needed to accommodate the PV panels. FSEC’s PV group laid out a 7 kW
PV system that included 4.5 kW’s of flat roof panels
(unique for a residential application) and sent information
to the architect. This activity ended in 2002 with no
home construction.
- Tommy
Williams Homes
Gainesville, FL
Category A, 19 Homes completed, 231 ongoing
This
builder has gone from Florida energy building code minimum
homes to being committed to build over 250 homes in two
new sub-divisions that meet the BA goal of a HERS score
of 88.6 or above. Each home will be serviced with a "right-sized" Seer
14 heat pump with a variable speed air handler, double
pane low-E windows with a SHGC of .36 or less, passive
OA system and a programmable thermostat. Each home will
be performance tested and commissioned.
- Top
of the World Retirement Community
Gainesville, Florida
Category B, 212 Homes
Technical Support by BAIHP Subcontractor: Florida
H.E.R.O.
Florida H.E.R.O. worked with project managers in charge
of On Top of the World Central, a retirement
community in Ocala developed by Sidney and Kenneth Colen
who have built 15,000+ homes for senior citizens and
have a commitment to developing communities that meet
the needs and desires of that unique population.
Project managers of On Top of the World Central have
every home performance tested for duct and whole house
air tightness. Other features of the homes are summarized
in Table 24.
This is the largest plotted sub-division in Florida,
with over 24,000 homes slated to be built. Top of the
World has gone from code minimum construction to Energy
Star.
Table
24 On Top of the World Characteristics |
Component |
Specification |
Conditioned area |
1120-2093 sq. ft. |
HERS Score |
86-89 |
Mechanical and System |
Engineered and right
sized systems
Engineered duct design |
Heating |
Standard 80% AFUE furnace |
Cooling |
SEER 12 AC |
Ducts |
Mastic sealed and tested |
Duct Leakage |
CFM25
out < 5% of
AHU flow |
Wall |
Block with steel interior
framing |
Windows |
Double pane |
- Trinity
Construction
Corporation
Coral
Springs, Florida
|
Figure 40
Panel forms on forming bed. |
Trinity
Construction
Corporation is
a large shell
contractor serving
Florida homebuilders.
Faced with increasing
demands for higher
quality, lower
cost and more
timely delivery,
Trinity is actively
exploring innovative
alternatives
to conventional
concrete block
construction,
the predominant
homebuilding
technology in
the central and
south Florida
market. Trinity
operates a pre-cast
concrete panel
production facility,
in South Bay,
Florida where
concrete panels
are pre-cast (Figure
40), transported
to the construction
site, and quickly
assembled using
a construction
crane (Figure
41). The
UCF Housing Constructability
Lab (HCL) was
asked to assist
Trinity in improving
the current panelizing
process by incorporating
lean production
principles such
as "just
in time" materials
handling.
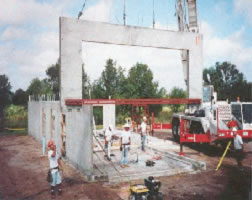 |
Figure 41
Setting pre-cast concrete wall
panel. |
Preliminary
research involved
extensive observation
and analysis.
Value stream
mapping, a process
to isolate waste
and production
efficiency opportunities,
identified activities
that contributed
value to the
customer as well
as activities
that added little
or no value.
Material handling
and rework were
primary contributors
to the 47% of
labor consumed
by non-value
added activities.
Once construction
started, the
flow of value-added
activity was
routinely interrupted.
Poor access to
materials and
tools, rework,
ill-defined process
flows, and workforce/1
st line supervision
issues were contributing
factors. To address
these issues,
BAIHP researchers
utilized lean
production principles
- challenging
non-value added
activities and
removing the
obstacles to
continuous production
flow. Recommendations
addressed issues
of organization/communication,
structured procedures
and work flow,
material handling,
and off-line
sub-assembly.
Table
25 Panel Productivity in Square Foot of Wall per
Labor Hour |
Process Phase |
"Tested
Sample"
Process
|
Potential
Process Results
|
Pilot
Test
Process
|
Productivity
Increase During Test
|
Layout |
53 |
152 |
91 |
72% |
Prep |
52 |
149 |
79 |
52% |
Pouring |
146 |
211 |
296 |
103% |
Lifting |
75 |
440 |
75* |
0% |
Total |
17 |
49 |
25 |
47% |
*Not altered
during pilot test. |
To test the
recommendations,
Trinity allowed
BAIHP researchers
to perform a
3-day pilot test.
The test involved
a single house
consisting of
25 panels. The
panels had a
total of 21 window
and door openings
and a gross wall
area of 3,119
ft 2. The first
day was used
to organize and
train the test
production team.
The second and
third days were
dedicated to
production. All
25 panels were
produced. Productivity
increased (Table
25) for
all observed
activities. Lifting
productivity
was not observed.
Conservatively
assuming that
lifting activity
will remain at
historical levels,
overall labor
productivity
increased by
47% during the
Pilot Test. If
lifting productivity
is assumed to
increase at the
average rate
observed for
the other activities,
overall productivity
increase of the
Pilot Test would
be 68%. Not all
recommendations
could be realized
during the test.
Some equipment
and personnel
issues could
not be resolved
on a short-term
test basis. This
suggests that
the true potential
is significantly
greater than
that observed
during the Pilot
Test – possibly
approaching 200%
increase in labor
productivity.
Corresponding
cycle time reductions
are estimated
to be 20-25%.
The BAIHP research
team recommended
that Trinity
precede with
implementation
of the lean production
recommendations.
In addition to
the technical
recommendations,
the research
team also made
recommendations
involving worker
empowerment,
dealing with
the heat and
sun, and material/equipment
availability.
Potential future
research areas
include covers
for the production
area, on-site
factories in
new home developments,
and factory installed
wall insulation.
This successful
pilot test has
given Trinity
the opportunity
to develop a
competitive advantage
in the housing
construction
market and a
solid foundation
to gain dominance.
- Vincent
Village
Richland, Washington
Vincent Village is a 49 home rental community, located
in Richland, WA. All of the homes are small, single section
HUD Code homes, heated and cooled by Insider heat pumps.
Half the homes were built to Super Good Cents standards,
the other half were not. Metered utility data indicate
average yearly savings of $241 for the SGC homes. (See
also Appendix D, WSU)
- WCI
Communities, Inc.
Bonita Springs, Florida
Category A,
2 Houses
Technical Support by BAIHP Researcher Eric
Martin
Awards: 2004 SEBC Green Demonstration Home
Aurora Award
2004 SEBC Green Production Home Aurora
Award
2004 SEBC Green Home Grand Aurora Award
2004
Energy Value Housing Award, Silver Medal , Custom /Hot-Humid
Climate
2004 NAHB America’s Best Builder, 501-plus
closing category
Builder/Developer WCI Communities
continues to embrace green building by having constructed
over 100 homes to the Florida Green Home Standard,
including two very high performance demonstration homes.
They received the second ever Florida Green Land Development
certification for their Venetian Development in Venice,
FL in which all homes constructed within will also
be green certified. Upon build-out, this will amount
to over 1,000 homes.
WCI Communities architecture division is providing
architectural services for the 2006 New American Home.
During a meeting at FSEC in July 2004, elements of green
certification of this home were discussed. The principal
architects have completed the green certification training
offered by FSEC, and the project is on track to receive
the Florida Green Home Designation once complete.
|
Figure 42 WCI
Home in Evergrene
Community, Palm Beach Gardens
(FL), HERS Score = 92. |
WCI is also planning another high performance demonstration
home in a new community being developed on the south
east coast of Florida. They have expressed interest in
this being a Zero Energy home, and BAIHP conducted training
in October 2004 for WCI staff and subcontractors providing
an overview of ZEH design strategies and implications
to the WCI architecture staff.
During the fourth budget period, in November of 2002,
BAIHP staff members were planning to meet with WCI to
discuss a partnership. Because of their corporate environmental
mission, WCI plans to build a significant number of homes
to the Florida Green Home Designation Standard and has
requested the help of Building America to ensure a systems
engineering approach, to conduct efficiency monitoring,
and to offer staff training. WCI constructs approximately
2,000 homes per year across south Florida. In 2002 they
committed to having houses incorporate a variety of green
principles. In some WCI communities, every home will
meet the Florida Green Standard.
FSEC received sample home plans and conducted an energy
analysis using EG USA. Recommendations were adopted by
WCI (Table 26) for a model “green home” in
the Evergrene Community (Figure 42) in Palm
Beach Gardens (FL). BAIHP monitored progress on the prototype
and installed monitoring instrumentation in April 2003
(fifth budget period).
The home and the instrumentation were completed in
August 2003. A device called WebDAQ was installed, which
acts as a server to provide an internet web page to display
real time data as part of WCI's community education approach.
WCI maintains a website dedicated to the home at www.greengeneration.org.
In September 2003, WCI held a grand opening at Evergrene.
Staff from BAIHP and the DOE Atlanta Regional Office
attended the event which included tours of the home and
a program of distinguished speakers such as local government
and business leaders.
This
prototype “green home” received the
highest score to date on the Florida Green Home Designation
Standard. With a HERS score of 92, it is estimated to
save 31% compared to the Building America benchmark home
and 38% compared to the HERS reference home on a whole
house basis.
In February 2004, FSEC staff visited the Venetian Development
in Venice, FL developed and built by WCI Communities,
Inc. Over 1,000 homes will be constructed in Venetian,
and all will meet the requirements of the Florida Green
Home Designation Standard.
Table
26 WCI Evergrene Community - Green Home Model Specifications |
Conditioned Area |
1460 sq ft |
HERS Score |
92 |
Envelope |
Above-grade Wall |
ICF - first floor; 2X6 with Icynene
- second floor |
Attic |
Unvented, insulated at roof deck w/Icynene |
Roof |
Tile |
Windows |
Laminated Impact Resistant with SHGC
= 0.42 |
Equipment |
Ducts |
Sealed with mastic; Located in unvented
(Insulated) attic |
Heating & Cooling |
Variable speed SEER 15 with strip electric
heating |
Thermostat |
Programmable thermidistat |
Water Heater |
Conventional gas unit with EF=0.62 |
Lighting |
CFL and fiber optic lighting with occupancy
and daylight sensors |
Appliances |
Energy Star |
Indoor Air Quality |
Extensive VOC source control through
paint, cabinet, and counter top selection |
Ventilation |
Passive fresh air duct to mechanical
closet; Whole house filtration with UV sterilization |
Green Features |
Lumber |
All lumber certified sustainable, treated
lumber is ACQ, other lumber is engineered |
Water Conservation |
Dual flush toilets, automatic faucets,
drought tolerant landscape, micro irrigation, rainwater
harvesting. |
Resource Efficiency |
Eco-friendly flooring and finishes
Construction waste management plan
|
In
addition, WCI constructed another "ultra green" model.
WCI consulted BAIHP during the initial planning stages,
and this home was expected to have higher performance and
contain more green features than the Evergrene Community
home. WCI took the initiative to develop in-house expertise
and capabilities in this area and needed much less support
from BAIHP. BAIHP did involve IBACO, another BA Team, to
help develop an advanced lighting design.
|