BAIHP
Research: B. Site Built Housing Research Cont'd
- Eastern
Dakota Housing Alliance (EDHA), Applegren Construction
Grand Forks, North Dakota
Category A, 10 Homes
Category B, 13 Homes
Technical Support by BAIHP Researcher, Dave Chasar
Awards:
North Dakota Housing Finance Agency’s
Champion of Affordable Housing Production Award
Paper:
Chasar, D., Moyer, N., Chandra, S., Rotvold, L., Applegren,
R., "Cold Climate Case Study; High
Efficiency North Dakota Twin Homes," Performances
of Exterior Envelopes of Whole Buildings IX International
Conference, Clearwater Beach, Florida, December 2004.
Table
42 Completed Selkirk Homes |
. |
Phase I |
Phase II |
Phase III |
Number of Homes |
4 |
4 |
4 |
Completion Date |
Mar-03 |
Jan-04 |
Aug-04 |
HERS range |
88 – 90 |
92.5 |
88 – 89.5 |
BA Benchmark range |
25 – 30% |
40% |
TBD |
The Eastern Dakota Housing Alliance plans to build
20 multi-family and single-family dwellings on Selkirk
Circle in Grand Forks, North Dakota. Twelve homes have
been completed to date and four more are currently
under construction. Four
Phase I units completed in March of 2003 had HERS ratings
between 88 and 90 with whole-house savings of 25 to 30%
against the Building America benchmark. Four Phase II
units completed in January 2004 had HERS of about 92.5
and whole-house savings of 40%. The Phase II efficiency
boost comes from the addition of a whole-house tankless
gas water heater and R10 sheathing on exterior walls.
Lower HERS scores (88.3 – 89.5) on the Phase III units
was primarily due to electric resistance water heating
and higher overall duct and envelope leakage. All units
have ventilation air brought to the air handler return
plenum with 10 of 12 units utilizing heat recovery ventilators
(HRVs).
|
Figure
75
Two completed
Phase III units (Dec 2004) |
Phase III Testing
A new floor plan was used on the Phase III homes featuring
a split level design instead of a full, below grade basement
and attached rather than detached garages. Another major
difference between these units and previous designs was
the location of the air handler in a utility room that
opens into the garage. As with previously tested homes,
total leakage was very high and concentrated mostly on
the return side where duct pathways were partially constructed
from building cavity spaces. Duct leakage to out, which
was nearly zero in previously tested homes, was substantially
higher in the Phase III units. Duct tester results showed
that the ratio of duct leakage to out (at 25 Pascals) to
conditioned floor area (or Qn) ranged from 0.05 to 0.09.
As with previous phases, all Phase III units had high efficiency,
sealed combustion gas furnaces.
Table
43 Selkirk Split-level Twin Home Specifications – Phase
III |
Conditioned Area |
1850 sq. ft. (including
basement) |
Above-grade Walls |
Wood Frame (R15+R10 sheath) |
Sub-grade Basement Walls |
R22 Insulated Concrete
Forms |
Ventilated Attic |
R-49 |
IG Vinyl Windows |
U-0.34, SHGC-0.33 |
Sealed Combust. Gas Furnace |
60kBtu, AFUE-92.6 |
Strait-cool AC |
2-ton, 10 SEER |
50 Gal Electric Water
Heater |
EF 0.86 |
Thermostat |
Programmable |
Lighting |
85% Fluorescent |
Ventilation |
70% HRV |
Each Phase III unit was tested individually for envelope
tightness. Leakage was higher overall compared to Phases
I and II, but this was expected due to the greater exterior
surface area created by the attached garage design.
Table
44 HERS Scores and Envelope Leakage
Test Results |
Unit |
HERS |
CFM50 |
ACH50 |
ACH |
C |
n |
R |
1002 |
89.5 |
779 |
3.12 |
0.11 |
22.7 |
0.90 |
0.98 |
1010 |
88.3 |
970 |
3.85 |
0.32 |
100.4 |
0.58 |
0.97 |
1018 |
89.0 |
999 |
4.00 |
0.24 |
64.2 |
0.70 |
0.99 |
1026 |
89.1 |
783 |
3.14 |
0.16 |
38.9 |
0.77 |
0.99 |
Notes:
- ACH50 calculation includes area of conditioned
basement |
Discussion on Next Set of Homes
Four Phase IV homes are currently under construction
utilizing the same floor plan and envelope design as Phase
III. Plans include the use of high efficiency gas water
heaters (probably tankless) and a central return duct system
designed to reduce duct leakage (both total and to out).
Return air relief for bedrooms will be incorporated into
hallway walls with either a high-low grill system or pass-through
grills with sound and light baffles. Plans also include
relocating air handlers within the conditioned space instead
of in a room attached to the garage. This should substantially
reduce duct leakage to out.
Recommendations include:
- Central return located near thermostat in center of
home
- Sealed ductwork from central return to air handler
- Avoid use of building cavities as air pathways
|
Figure
76 East side
of Selkirk Circle,
Phases III & IV |
Building Science Issues:
- Combining
space heating and hot water with a central gas boiler.
Since air conditioning is still a requirement, an air
handler with an hydronic heating coil will be required.
- If only 2 of 4 units are fitted with a combined system
it offers the opportunity to compare the efficiency of
this system over another unit with separate space and
water heating through monitoring.
- David Duly of Pilkington
glass has offered to work with FSEC to determine the
benefit of high solar gain glass which could provide
substantial savings on space heating. Window orientation
and shading are important factors that may work favorably
with the remaining south-facing home sites on Selkirk
Circle.
BAIHP will be conducting Building America benchmarking
analysis of these homes and producing Energy Star ratings
of the four Phase III homes as well as the Phase IV units
upon completion in spring/summer of 2005.
- Zero
Energy Affordable Housing, ORNL and Loudon County
Habitat for Humanity
Lenoir
City, Tennessee
Category A
Research
by ORNL with BAIHP Support
|
Figure 77 Local
sponsors in front of 2nd ZEH built by Loudon County
HFH in partnership with ORNL. FSEC provided monitoring
for the 1 st and 4 th ZEHs . |
In partnership with Oak Ridge, BAIHP has instrumented
two a zero energy homes (ZEH) built by Loudon County
(TN) HFH in partnership with Oak Ridge National Laboratory. (Figure
77) See description in the Technical Assistance section
of this report under Habitat for Humanity, Tennessee,
Loudon County.
Data is available on-line at www.infomonitors.com
. A paper on the study was submitted to the Buildings
IX conference by Jeff Christian (ORNL) and David
Beal (BAIHP-FSEC).
Federation
of American Scientists’ Rasbach
Provident Home
BAIHP is assisting FAS and builder Joe Ecrette with
envelope and mechanical system design on this home
built with cementitious faced SIP panels. The home
serves as a demonstration of an affordable, efficient
home that is also well-suited for areas prone to seismic
disturbance. A preliminary HERS score of 89 is estimated.
BAIHP
will provide data monitoring design assistance, equipment
and installation to document energy savings. Data collection,
processing and archiving will be provided through FSEC’s
Infomonitors service, online at www.infomonitors.com.
- Hurricane
Retrofit Research
Many homes in east central Florida suffered serious
damages in 2004 as a result of the hurricanes. We have
identified four families who would be willing partners
for a U.S. DOE funded project to showcase cost effective
energy efficient retrofits.
All
homes are within 30 miles of FSEC and none are “luxury” homes.
All four homes have undergone a pre retrofit analysis
and testing to determine the current energy usage profile
and expected energy savings, enhanced comfort , indoor
air quality and related benefits. Pre retrofit tests
included blower door, duct blaster, pressure mapping
and air conditioner system performance measurement.
In addition, lighting and water heater and other opportunities
will be assessed. All homes will be analyzed by the
Energy Gauge USA software to quantify the expected
energy savings. Pre and post utility bills will be
documented for all homes.
The owners have agreed to keep track of the costs
and share them publicly.
Post retrofit, Energy Gauge USA analysis will be conducted
on all homes and energy savings computed relative to
the Building America benchmark. This will require blower
door and duct testing of the home post retrofit. A
one to two page case study will be prepared for all
four homes. Some homes will be monitored in more detail
to examine key performance areas. The four homes offer
a range of retrofit options and will provide good data
on the costs and benefits of effective retrofit strategies
in hot-humid climates.
- Apartment
Ventilation and Humidity Study with Sandspur Housing
Gainesville, Florida
In April and May of 2003, four of 111 newly built
apartments at the Brookside Apartment Complex were
evaluated for potential moisture problems. Characteristics
of the four apartments are summarized in Table
XX1. The ventilation strategy introduced untempreed
outside air to the return side of a central air handler.
Table
XX1 Apartment Characteristics |
Apt ID |
Floor |
Occupants |
RH Control |
Outside Air Flow |
Infiltration
(ACH50) |
Thermostat
Setting |
1 |
1st |
1 |
AC only |
25cfm |
2.8 |
Variable |
2 |
2nd |
2 |
AC only |
17cfm |
2.5 |
Variable |
3 |
2nd |
0 |
AC only |
27cfm |
3.2 |
76º |
4 |
1st |
0 |
AC only |
28cfm |
3.9 |
76º |
Sensors were installed in four apartments that monitored
Temperature and RH in three locations: the air handler
cabinet, the kitchen, and the master bedroom closet. The
readings from Apartment 2 were within recommended
guidelines in all living spaces monitored, with no changes
recommended.
Table
XX2 Apartment Results |
. |
Kitchen |
MB
CLoset |
Apt ID |
Temp
Av. |
RH Av. |
Temp Av. |
RH Av. |
1 |
71.9º |
54.3% |
71.7º |
62.0% |
2 |
76.0º |
47.6% |
76.9 º |
53.5% |
3 |
Invalid
data
(See Figure XX3) |
N/A |
N/A |
4 |
71.4º |
50.2 |
N/A |
N/A |
Note:
Data from the AirHandler senors were similar for
all four apartments (reflecting the extremes expected
in this locations with RH as high as 90% and 100%),
and was not pertinent to the living space temperature
and RH. |
The temperature in Apartment 1 was
lower than Apartment 2, the other occupied unit. The
readings were within the acceptable level for comfort
and mold control, but because the air conditioner ran
longer, it also had a longer period to remove moisture.
Inspection found that the windows were opened about 1
1/2”. When the occupant
(the maintenance man for the complex) was asked why, he
indicated that it was being done for “health purposes”.
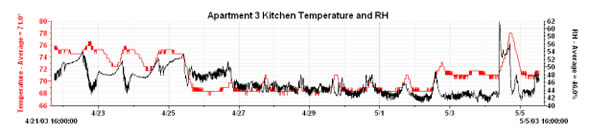
Figure XX3 Apartment 3 Kitchen
Temperature and RH
The master bedroom closet reflected the lower temperatures
of the kitchen but with a slightly higher RH level. The
higher RH level in this space was likely due to the closet
door being closed which would slow the passage of the dryer
kitchen air into the closet space.
The remaing apartments tested varied a large amount over
the period of test. Apartment 4 had wide swings
in temperature readings. With no significant period of
time in which the temperature was stable, it is assumed
that the AC was not running properly in this unit.
Apartment 3 is notable because this unit was
vacant and its temperature should have stayed stable within
three degrees. The good RH levels were likely due to the
longer Air Conditioner run times required to maintain the
low temperature.
Outside Temperature and RH: The
test period was during the beginning of Florida summer
temperature and RH trends. Daytime high temperatures
reach into the low 90’s with associated high RH
levels in the afternoon. These cycles are reflected in
the data collected, the most obvious of these being the
apartment 2 closet (Figure
XX5) where daily outdoor temperature peaks mimic those
of the indoor temperature peaks .
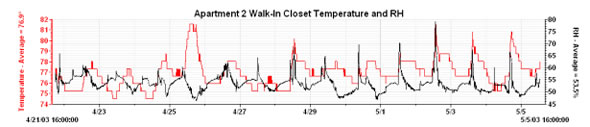
Figure XX5 Apartment 2 Walk-In
Closet Temperature and RH
Final observations: If all of the apartments
have similar characteristics to those of Apartment 1 and
Apartment 2, then no changes to lower interior RH levels
are required at this time. RH level averages are well within
the acceptable range – even in spaces where RH levels
tend to get rather high (i.e. – closet) validating,
at least preliminary the adequacy of the design principle
of using outside ventilation air as has been implemented
in these units.
Recommendations
- Educate those involved in the care and maintenance
of apartment complexes in basic principles of building
science.
- In future apartments locate a supply register in the
closet to provide better humidity control for this area.
- Check
Apartment 3 & 4 equipment for proper operation,
and calibration of thermostat.
|